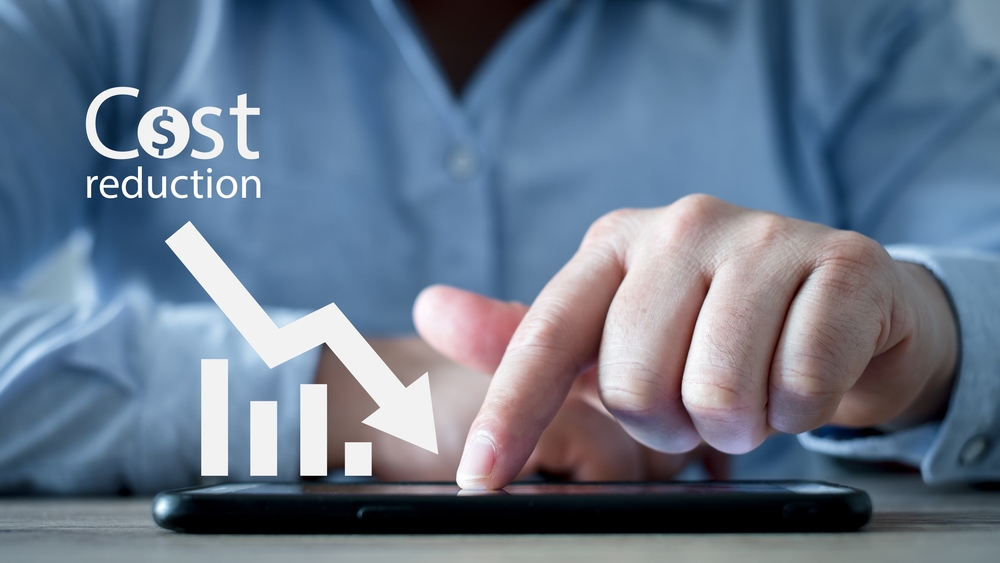
High operating costs continue to be a major challenge for wood product manufacturing companies. Managing these expenses effectively is essential for maintaining profitability and growing your business. The wood manufacturing industry is characterized by its reliance on raw materials, labor-intensive processes, and energy consumption. This makes controlling operating expenses a critical factor for success.
Finding ways to reduce costs without compromising on quality or productivity can be difficult. Traditional methods of cost management often fall short of providing the comprehensive oversight and agility needed to respond to market demands and operational inefficiencies. This is where an Enterprise Resource Planning (ERP) system can make a significant difference.
Wood product manufacturers must gain control over their biggest cost drivers and identify opportunities for savings. This article will discuss key wood product manufacturing costs and how ERP systems can reduce these expenses and drive efficiency across the organization.
State of the Wood Product Industry
There is good news abounds for the wood product manufacturing industry, however. It has been steadily recovering from pandemic-era lows. According to a 2024 Wood Manufacturing Global Report, the market is expected to grow from $465+ billion in 2023 to $467+ billion in 2024. By 2028, it is projected to reach over $521 billion. Some predicted growth trends are attributed to the increase of more sustainable practices, advanced manufacturing technology, and digitalization of the supply chain.
The building and construction industry is expected to grow. With new homes, apartments, and business construction comes the need for doors, cabinetry, furniture, and flooring. The demand for wooden furniture is predicted to increase the most, while cabinetry and flooring remain in high demand.
Every wood product manufacturer has their unique challenges and opportunities, but they all want to cut costs and work more efficiently. An ERP system can be a valuable tool in achieving these objectives.
Key Cost Drivers in Wood Product Manufacturing
Many factors drive up wood product manufacturing operating costs. They include the cost of materials, labor, and energy needed for production. Plus, necessary expenses from transportation to responsible waste management can take a large bite out of the bottom line. Understanding these cost drivers is crucial for manufacturers to find ways to reduce expenses to improve profitability.
The highest wood product manufacturing costs typically fall into the following categories:
Overhead
Overhead costs in wood product manufacturing encompass a wide range of expenses essential for the facility’s overall operation. These costs include utilities such as electricity, water, and heating that are necessary for maintaining the working environment. Insurance costs are significant, covering the facility, equipment, and employee health and safety. Effective management of these overhead expenses is important for maintaining operational efficiency and profitability.
Energy
Wood product manufacturing energy costs are quite substantial due to the energy-intensive nature of the production processes. Key operations such as sawing, drying, milling, and finishing require significant amounts of electricity and fuel. Manufacturers often face high utility bills and fluctuations in energy prices can further strain their budgets. Implementing energy-efficient technologies and practices can help mitigate these costs, however, optimized energy management is vital to control costs.
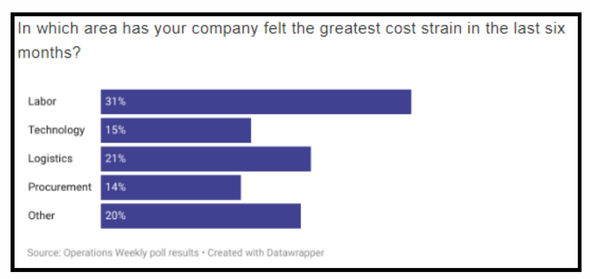
In a recent Supply Chain Dive manufacturing readers poll, 31% said labor was their largest cost strain. (Source: Supply Chain Dive Newsletter)
Raw Materials
Raw material costs are a necessary expense for wood product manufacturers. High-quality lumber, veneers, and other essential materials are subject to price fluctuations that often soar. Efficient sourcing, logistics, and inventory management strategies are crucial to mitigate these expenses, ensuring a steady supply of materials at competitive prices.
Labor
Skilled workers are needed for cutting, assembling, and finishing in wood product manufacturing, resulting in higher labor costs. These costs encompass not only wages but also benefits, such as health insurance, retirement plans, and paid leave. Additionally, manufacturers must invest in ongoing training and development programs to ensure workers remain adept with new technologies and processes. Personnel recruitment further contributes to the overall labor expense, making it a critical area for cost management.
Equipment and Maintenance
Equipment and maintenance expenses for wood product manufacturers can be substantial. This is due to specialized machinery that is required for various stages of production, including sawing, planing, shaping, and finishing. These machines need regular upkeep and occasional repairs to ensure they operate at optimal efficiency to meet production demands. Investing in new equipment or upgrading existing machinery to incorporate advanced technologies can be necessary to improve productivity.
Logistics and Transportation
Logistics and transportation expenses continue to rise for hauling both raw materials and finished goods. Raw materials like lumber often require specialized handling and transport, adding to logistical complexities and costs. Finished wood products, often bulky or fragile, necessitate careful planning for shipping. Efficient logistics management is crucial for minimizing costs and ensuring timely delivery and customer satisfaction.
Regulatory and Waste Management
Regulatory and waste management costs encompass adherence to stringent environmental regulations and standards. These expenses include acquiring permits, conducting environmental impact assessments, and implementing measures to mitigate the ecological footprint of operations. Proper handling and disposal of wood waste and by-products add to the overall operational expenditure in maintaining environmentally sustainable practices.
How ERP Systems Cut Operating Costs
While they can’t help with the cost of materials, ERP systems do help wood product manufacturing companies realize considerable savings on their operating costs. Informative data analytics, automated processes, and optimized production scheduling are just a few ways they contribute. Let’s explore these and several other ERP system features that can help your bottom line.
Data-Driven Decision Making
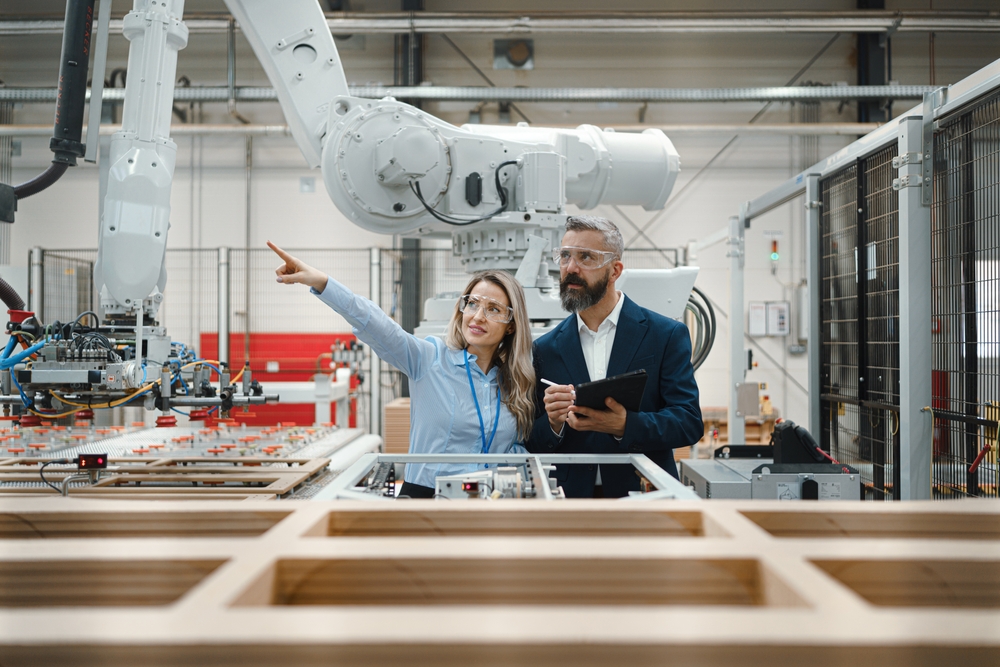
Robust analytics and reporting features in Frontier ERP allow your company to dive deep to uncover cost-saving opportunities.
Comprehensive Reporting
ERP systems provide detailed insights into operational KPIs, enabling informed decisions that reduce costs. Comprehensive reporting helps identify inefficiencies and areas for improvement, driving cost savings across the organization.
Predictive Analytics
Using data to forecast trends and plan accordingly minimizes risks and optimizes resource allocation. Predictive analytics help manufacturers anticipate market changes and adjust their strategies, reducing costs and maximizing opportunities.
Streamlined Supply Chain Management
Supplier Integration
ERP systems facilitate better communication and coordination with vendors and suppliers. This integration can lead to bulk purchasing discounts, just-in-time inventory, and reduced procurement costs. Improved supplier relationships and the ability to monitor vendors also ensure a more reliable supply chain for those in wood product manufacturing.
Automated Processes
ERPs enhance supply chain efficiency, decreasing lead times and the cost of procurement. They automate the entire procurement process, from material planning to purchase order creation and invoice processing. That means fewer administrative tasks and also reduces manual errors, accelerating the purchasing cycle.
Optimized Logistics Management
ERP software can integrate with popular logistics applications enabling manufacturers to plan more efficient routes, consolidate shipments, and reduce transportation costs. An ERP system can also help you track shipments and provides automatic status updates for customers.
Improved Inventory Management
Stock Level Optimization
ERP software helps you maintain optimal stock levels by providing real-time inventory data. This prevents overstocking, which ties up capital. Overstocking also increases storage costs and stockouts, which can disrupt production schedules and lead to lost sales. By optimizing stock levels, manufacturers can reduce carrying costs and minimize waste.
Real-Time Tracking
ERPs help you say goodbye to emergency orders and last-minute purchases, which often come at a premium cost. With real-time tracking, an ERP ensures that you always have up-to-date inventory information. This allows wood product manufacturing companies to make informed decisions about purchasing and production. Additionally, ERP software can streamline supplier management, as mentioned above, helping to negotiate better terms and prices.
Enhanced Production Planning and Scheduling
Efficient Resource Utilization
An ERP system ensures that materials, machinery, and labor are used efficiently. Automated production planning and scheduling reduces idle time, minimizes waste, and ensures proper resource allocation. Automating the entire production process, from order entry to delivery, reduces manual intervention and associated costs.
Accurate Demand Forecasting
ERPs use historical data and predictive analytics for production tracking and to forecast demand accurately. Wood product manufacturers can adjust production to match market demand, reducing extra work and costs from unsold inventory.
Equipment Maintenance and Management
With ERP software, you can schedule regular equipment maintenance outside of regular production scheduling. This keeps the production line moving while also lessening the risk of unexpected breakdowns and costly repairs. By tracking equipment performance and maintenance history, manufacturers can extend the lifespan of their machinery and avoid unnecessary capital expenditures.
Labor Cost Reduction
Automated Processes
Automation of repetitive tasks reduces the need for manual intervention, lowering labor costs and minimizing human error. This allows employees to focus on more value-added activities, increasing overall productivity and accuracy.
Efficient Labor Management
ERP software optimizes workforce scheduling and tracks labor performance. This reduces overtime expenses and improves labor productivity. ERPs improve workforce management by automatically scheduling tasks and tracking labor hours. This leads to more efficient utilization of labor resources, reducing idle time and labor costs.
Energy Efficiency
Optimized Machine Use
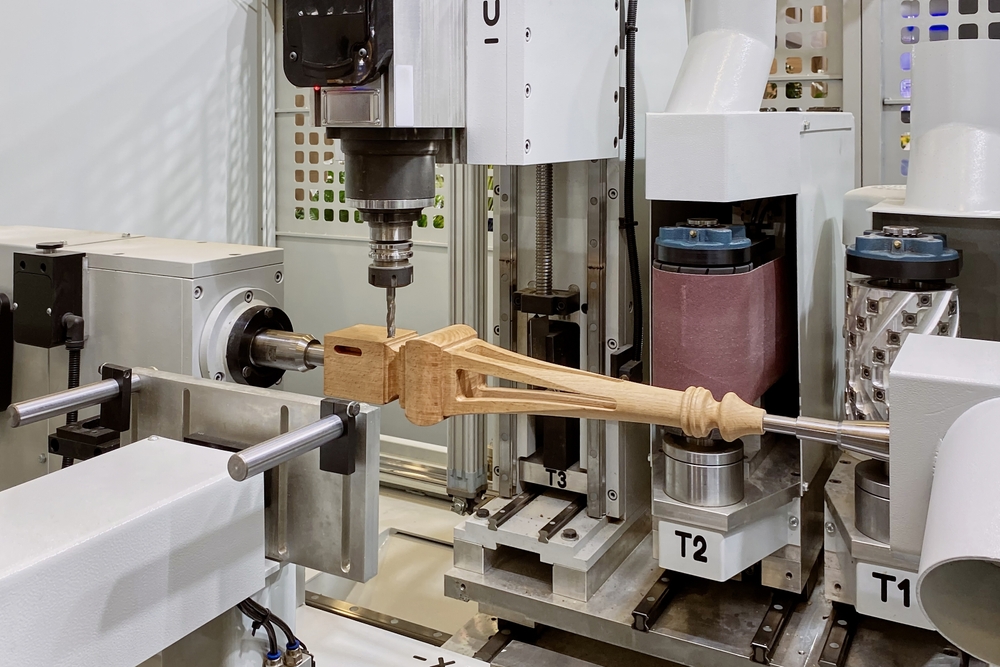
Frontier ERP cut mapping works seamlessly with machine-cutting equipment interfaces to streamline your automated processes. This results in saved labor and reduced cut waste.
ERP systems ensure that machinery is used efficiently, reducing energy consumption and maintenance costs. By tracking machine usage, manufacturers can schedule preventive maintenance, avoiding costly breakdowns and downtime as mentioned above.
Monitoring and Reporting
By monitoring energy usage across the wood product manufacturing process, ERP systems identify areas for improvement and cost savings. Manufacturers can then implement energy-saving measures and track their impact, leading to reduced energy costs.
Waste Reduction and Compliance
Effective Waste Management
ERPs provide more efficient production processes that support lean manufacturing and waste management. Wood product manufacturers can therefore minimize waste disposal costs and improve your environmental footprint.
Precise Cutting and Processing
Improve accuracy in cutting and processing with ERP machine cutting features that reduce material waste and enhance yield. This precision ensures that you get the most out of your raw materials, lowering costs and increasing profitability.
Regulatory Compliance
ERP system tools enable waste disposal reporting requirements for tracking and documenting governmental and environmental adherence. Report compliance helps wood product manufacturers reduce the risk of fines for non-compliance.
Customer Relationship Management (CRM)
Improved Order Processing
ERPs enhance accuracy and speed in order fulfillment, improving customer satisfaction and reducing return costs. Frontier ERP includes built-in CPQ software that automatically generates quotes and pricing based on ERP product configurations. Streamlined order processing eliminates order errors and ensures that customers receive their products on time.
Better Field Service
Access real-time data from all departments with ERP software to keep your field service costs at bay. This central database supplies field service teams with updated customer, product, warranty, and service contract data. Having access to service allowances and billing rates ensures proper invoicing. This improves cash flow, reduces miscommunication, and helps maintain customer loyalty.
Conclusion
In conclusion, despite the growth in the wood product manufacturing industry, businesses continue to struggle with operating costs. ERP systems provide time-saving automation features and streamlined processes for more efficient operations. Not only do ERPs help you battle rising costs at present, but they also provide long-term savings solutions that can lead to business growth.
Frontier ERP is the leading software provider for make-to-order manufacturers. With our streamlined processes and innovative features, your wood product manufacturing company can become more efficient and increase your bottom line. Frontier integrates seamlessly with our shipping application partner, Varsity Logistics, for optimized logistics that save you even more time and money. To learn more about how we can optimize your shipping and logistics, join our Supply Chain Tech Masterclass on July 31!
Would you like to learn more about Frontier ERP’s cost-saving features? Contact us today or visit us at North America’s Largest Woodworking Event | Tuesday–Friday | August 6–9, 2024!