
Custom cabinet manufacturing involves many different processes from the initial quote to the finished product. One such process is production tracking. Tracking isn’t just about keeping records; it’s about analyzing operations, maintaining quality, and meeting customer demands effectively. Efficient production tracking is essential for cabinet manufacturers to monitor and cost-effectively control their operations.
Whether you’ve been manufacturing cabinets for a long time or just starting, monitoring your manufacturing processes is important. Read on for answers to the most common questions about cabinet manufacturing production tracking.
What is Production Tracking?
Production tracking in custom manufacturing refers to the process of monitoring and managing various stages of the production cycle. This ensures efficient and effective manufacturing operations. It involves tracking the progress of raw materials, work-in-progress (WIP), and finished goods as they move through the production process. Overall, tracking in manufacturing enables you to optimize production processes, improve efficiency, maintain quality standards, and meet customer demands effectively.
What Should I Track?
As a make-to-order cabinet maker, you need to track various steps in the building process. This ensures that the order meets client specifications while maintaining quality standards. Note that tracking often involves other departments that affect the production process.
- Quotes and Orders: Track sales orders from initial quote through to completion, including order details, specifications, and any changes requested by the client.
- Design and Consultation: Record design consultations with clients to understand their requirements, preferences, and any customization requests either directly or through your dealer. Tracking design revisions and client approvals ensures alignment with customer expectations.
- Material Procurement: Manage the procurement process for materials such as wood, hardware, finishes, and specialty items specified in the design. Tracking material orders, delivery schedules, and inventory levels shortens lead times and helps prevent delays and shortages.
- Scheduling and Workflow: Monitor scheduling and workflows on the shop floor, including task assignments, work progress, and resource allocation. Tracking workflows ensures tasks and production stays on schedule. Production reports can be generated for analysis and improvements as well.
Frontier ERP provides extensive data analytics for detailed report generation for production tracking and more!
- Cutting and Machining: Trace the cutting, shaping, and machining of raw materials to create cabinet components. Recording cutting lists, machine settings, and quality checks helps maintain accuracy and consistency in production.
- Assembly: Monitor the assembly process to ensure proper construction. Monitoring assembly steps and quality control checks helps prevent errors and rework.
- Finishing and Customization: Manage the application of finishes, stains, paints, or other customizations. Customization details and quality control tracing ensure the final product meets the desired aesthetic.
- Quality Control and Inspection: Conduct inspections at various stages of production to identify defects or deviations from the design. Quality control monitoring ensures the finished cabinets meet quality standards.
- Maintenance and Repairs: Record maintenance activities and repairs for machinery and equipment to ensure optimal performance and minimize downtime. Tracking maintenance schedules helps prevent equipment failures and disruptions to production.
Aren’t Manual Records Enough?
When production tracking records are kept manually, several common problems can arise, hindering efficiency, productivity, and overall performance. Here are some of the key issues that you may face:
- Inaccurate Data and Errors: Manual tracking methods, such as spreadsheets or paper-based systems, are prone to human error and waste resources. Data entry mistakes and inconsistencies can lead to confusion, delays, and miscommunication throughout the production process.
- Lack of Real-time Visibility: Without automated tracking systems, you might not be able to view production activities in real-time. It becomes challenging to monitor work-in-progress, identify bottlenecks, and make timely adjustments to optimize workflows.
- Poor Production Planning and Scheduling: Monitoring production on paper makes it difficult to create accurate production schedules that require access to orders, resources, and lead times. This can result in overbooking or underutilization of resources, missed deadlines, and inefficient use of labor and equipment.
- Inventory Management Issues: Inefficient tracing of materials and inventory levels can lead to problems such as stockouts, excess inventory, and inventory discrepancies. Without real-time inventory visibility, it becomes hard to maintain optimal stock levels and can result in production delays because of material shortages.
- Quality Control Challenges: Manual tracking systems make it challenging to enforce and monitor quality control processes effectively. Defects could be overlooked without automated quality checks, resulting in rework, scrap, or customer discontent.
- Ineffective Communication and Collaboration: A lack of streamlined tracking systems can lead to communication gaps and breakdowns between departments, suppliers, and clients. This can result in misunderstandings, delays in decision-making, and errors in production.
- Difficulty in Performance Analysis: Manual tracking makes it hard to analyze production data and identify areas for improvement. Without access to accurate and timely performance metrics, it may be difficult for you to implement process improvements and optimize operations.
- Compliance and Traceability Issues: Regulatory compliance is commonplace in cabinet manufacturing. Manual tracking may fail to ensure adherence to regulatory requirements. Additionally, without electronic traceability mechanisms, cabinet manufacturers may face challenges in tracking the origin of materials and components used in production.
- Increased Costs and Reduced Profits: Overall, inefficient production tracking processes can result in increased costs, decreased productivity, and reduced profits for cabinet manufacturers. Delays, errors, and inefficiencies lead to higher labor costs, wasted materials, missed deadlines, and ultimately, lower customer satisfaction and lost business opportunities.
Are All Tracking Systems the Same?
No, not all production tracking systems are the same. Some are not designed for your industry and exclude key processes. Other data collection software can be difficult to implement and challenging for users. Consider these key red flags when evaluating production tracking software for your company:
User Interface: Some production tracking software may have overly complex user interfaces with numerous menus, options, and features. This complexity can overwhelm users, making it difficult to navigate and use the software effectively. They may even be resistant to using the system altogether. Choose a user-friendly system.
Customization & Scalability: Tracking software that lacks customization options may not adequately cater to the specific needs and workflows of cabinet manufacturers. You may end up struggling to adapt the software to your processes, resulting in frustration and inefficiency. Look for scaleable software designed for cabinet manufacturers that includes a robust product configurator.
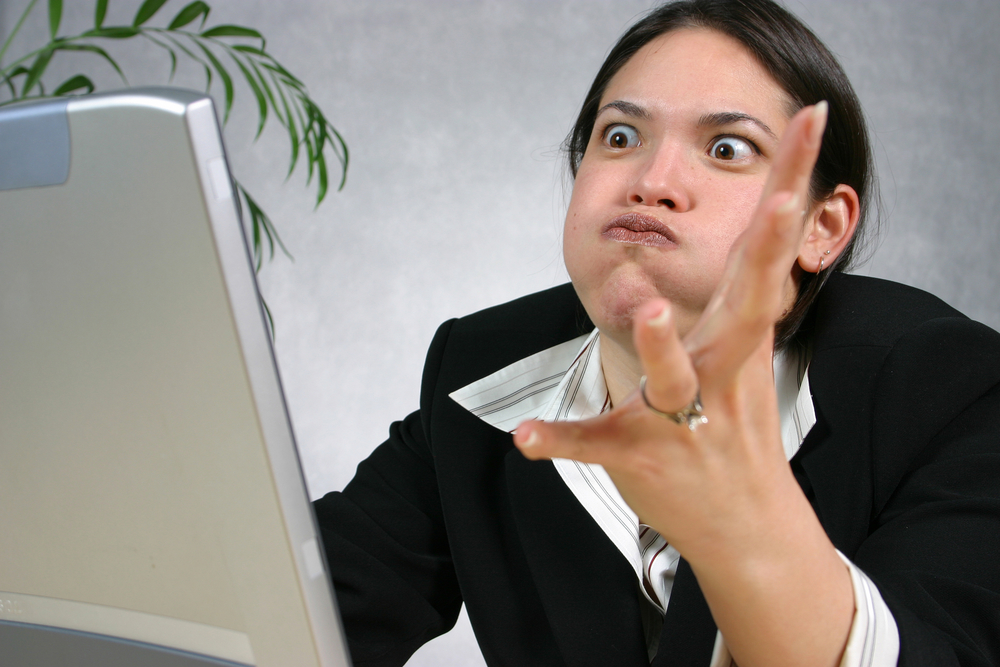
A poor user interface and integration errors can lead to major headaches for you and your employees.
Implementation & Integration: A new system should be easy to implement and integrate seamlessly with other company software. Inadequate integration methods lead to difficulties in transferring data, sharing information, and maintaining consistency across platforms. Vendors that offer clean integration methods and implementation processes are always the best option.
Support: Technical support is crucial for production tracking software. Untrained or inadequate support can hinder troubleshooting and minimize the software’s potential. Lack of responsive customer support can leave users feeling stranded when they encounter difficulties.
Input Methods: Consider production tracking software that supports RFID barcode scanning for paperless monitoring and greater efficiency. As stated before, manual inputs are time-consuming and create a higher risk of errors and inefficiency.
Workflows: Software with intuitive workflows eliminates illogical process sequences that can confuse users and impede productivity.
What is an ERP System?
ERP stands for Enterprise Resource Planning. ERP software systems integrate various core business processes and functions across an organization into a single system. These processes typically include finance, sales, human resources, production, inventory management, customer relationship management (CRM), and more.
ERPs provide a central data source that automates tasks and improves decision-making and resource allocation within the organization. They improve business processes, promote collaboration between departments, provide real-time information, and increase efficiency and productivity.
Do ERP Systems Streamline Production Tracking?
An ERP system can significantly enhance production tracking for custom cabinet manufacturing. It provides a centralized platform to manage and monitor various aspects of the production process. Here’s how an ERP system can help:
Streamlined Data Management: An ERP system consolidates production-related data, such as orders, materials, inventory levels, and production schedules, into a single database. This eliminates data silos and ensures consistency and accuracy in tracking information.
Real-time Visibility: Gain real-time visibility into production activities with an ERP system that allows you to track progress at each stage of production. Managers can monitor WIP, identify bottlenecks, and make informed decisions to optimize workflows.
Production Planning and Scheduling: Cabinet manufacturing companies benefit from efficient production planning and scheduling with an ERP. Integrated tools like CPQ software aid in creating production schedules based on order requirements, resource availability, and lead times. This helps you optimize production capacity, minimize idle time, and ensure timely delivery to customers.
Material Resource Planning (MRP): ERP systems can include MRP functionality to manage material requirements throughout the production process. You can track material availability, generate purchase orders, and optimize inventory levels to prevent shortages or excess inventory.
Workforce Management: ERPs facilitate workforce management by tracking labor hours, skills, and productivity levels. You can assign tasks, monitor employee performance, and identify opportunities for training or skill development.
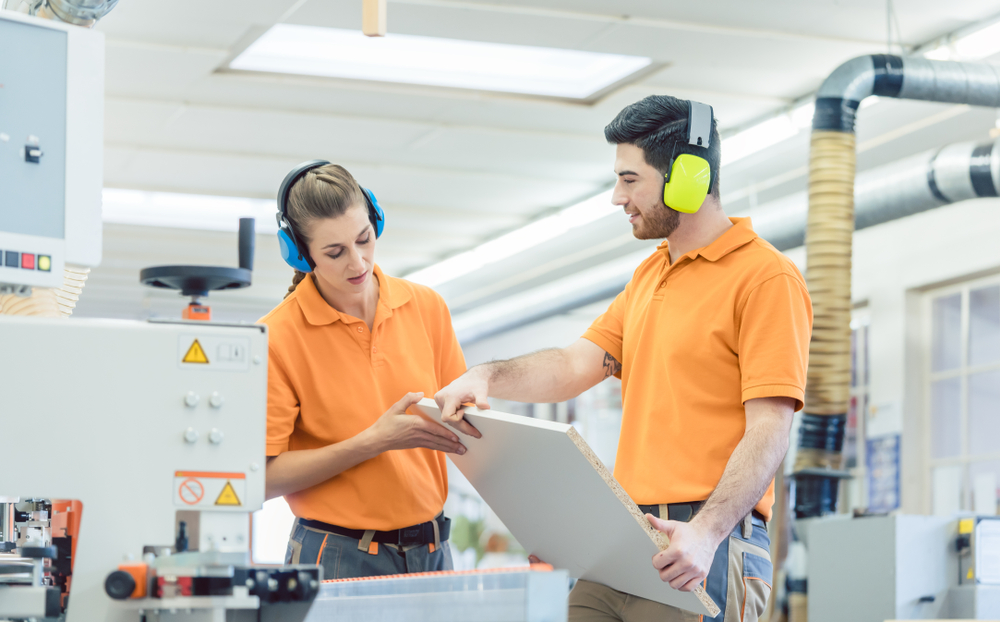
Track quality inspections and improve origin tracing with Frontier ERP.
Quality Control and Inspection: Support quality control and inspection processes with ERP tools to document and track quality standards, inspections, and any non-conformities detected during production. This ensures that your finished cabinets meet quality requirements and client expectations.
Traceability and Compliance: ERP systems enable traceability by recording the origin of components and materials used in production. This helps cabinet makers comply with regulatory requirements and facilitate recalls or audits if necessary.
Integration with Other Systems: The best cabinet manufacturing ERP software can integrate with other business systems. These include CAD/CAM software, accounting software, and dealer quoting systems. This seamless integration improves data accuracy, eliminates duplicate data entry, and enhances overall efficiency.
Data Analysis and Reporting: ERPs offer robust reporting and analytics capabilities, allowing you to analyze production data, identify trends, and make data-driven decisions. Managers can generate custom reports, track key performance indicators (KPIs), and gain insights to improve performance.
Overall, an ERP system serves as a comprehensive solution for your production tracking, enabling streamlined processes, improved efficiency, and deliver high-quality products to customers on time and within budget.
Frontier ERP Production Tracking
With decades of industry experience, Frontier understands the unique tracking requirements of custom cabinet manufacturers. That’s why our ERP software includes comprehensive shop floor management at its core with built-in production tracking and reporting capabilities. Detailed reporting for each production station ensures an informed approach to performance and efficiency optimization.
Our RFID reporting tool seamlessly generates reports on material movement, personnel activity, and transactions, enabling detailed tracking and analysis of stock and customer-specified products. You can confidently monitor production status, analyze scrap reasons, and identify manufacturing KPIs for process improvement through Frontier ERP.
Conclusion
In conclusion, production tracking is indispensable for the success of custom cabinet manufacturers. By monitoring each stage of the production cycle, you can manufacture quality products, meet deadlines, and optimize resources effectively. The adoption of ERP production tracking systems eliminates manual inefficiencies, provides real-time visibility, seamless integration, and user-friendly interfaces. This enables your company to stay competitive in a dynamic market.
Contact us today to learn more about Frontier’s production tracking capabilities and how we can optimize your cabinet manufacturing operations.