
In the realm of make-to-order manufacturing, businesses often grapple with the intricacies of managing their manufacturing processes. The landscape is dotted with a plethora of online solutions aimed at helping manufacturers trim costs and bolster their bottom line. Amidst this array of options, two foundational tools stand out as indispensable for optimizing operations: Enterprise Resource Planning (ERP) and Material Requirements Planning (MRP).
While both ERP and MRP are software systems tailored for manufacturers, they each fulfill distinct roles within the production cycle. ERP systems excel in integrating various aspects of a business, such as finance, HR, and supply chain management, into a cohesive platform. On the other hand, MRP systems focus specifically on materials and production planning, ensuring that the right materials are available at the right time for manufacturing processes.
Understanding the nuances and functionalities of ERP and MRP is key to streamlining manufacturing operations effectively. By delving deeper into how these systems operate and complement each other, businesses can unlock the full potential of their production processes.
Manufacturing Efficiency with ERP
At its core, ERP (Enterprise Resource Planning) systems for manufacturers are the backbone of business operations. A comprehensive manufacturing ERP encompasses accounting, order management, product configuration, customer data, inventory control, production scheduling, manufacturing operations, supply chain management, and more. The powerful software expedites data automatically across different departments, providing a comprehensive, real-time view of core processes and business activities.
The best ERP software for manufacturing provides an overarching framework with many management tools. This foundation enables efficient decision-making, resource allocation, and collaboration through complex large datasets and intricate processes. These factors make ERP software an ideal solution for manufacturing companies with complex business operations.
MRP Provides Precision Planning
Effective material planning is a cost-saving necessity in the manufacturing industry. MRP stands for Material Requirements Planning. Introduced in the early 1950s, MRP software was among the first computerized software programs developed to help companies increase manufacturing efficiency. It is still a critical component of a business, focused on managing inventory, scheduling production, and raw material availability.
MRP has been made even more powerful when brought in as part of a larger ERP ecosystem through integration. Its effectiveness relies heavily on the accuracy of data input into the system. Utilizing an ERP to feed the MRP software reduces the chances of errors and improves productivity.
For example, when a company receives a purchase order, it enters the ERP system. The ERP software captures the data and directly transfers it to the MRP tool. The MRP then swings into action by analyzing product demand, checking stock levels, and generating a precise production plan. This interaction ensures that the manufacturing process aligns seamlessly with broader business operations.
Bridging the Gap: How ERP and MRP Work Together
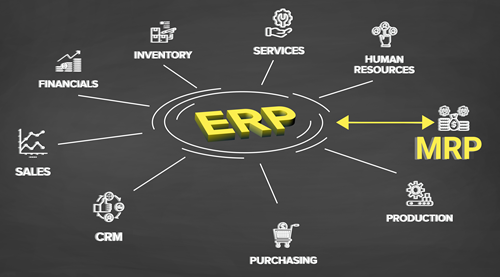
ERP and MRP systems work together to help businesses run more efficiently.
The beauty of this style of manufacturing management lies in how ERP and MRP complement each other. ERP provides the bigger picture – integrating departments and simplifying collaboration. MRP, as a subset, zeroes in on the granular details of material planning.
When they work together, information flows effortlessly throughout the organization. Customers place orders, ERP captures data, and MRP ensures that materials and production schedules align for optimal efficiency. This results in increased capacity and improved customer satisfaction.
The approach to material planning can vary so it is important to ensure that your ERP system is adaptable. Whether you are strategizing at the plant or product level, flexibility in your ERP is key.
Benefits of ERP and MRP Integration
Improved Visibility and Transparency
Integration plays a crucial role by offering unparalleled visibility into the manufacturing process. This comprehensive insight enables real-time monitoring of financial aspects, material flows within the production line, detailed production schedules, and identification of potential bottlenecks that could impact operational efficiency..
Enhanced Decision-Making
Accurate and up-to-date information plays a pivotal role in empowering decision-makers across various industries. By seamlessly integrating Enterprise Resource Planning (ERP) and Material Requirements Planning (MRP) systems, businesses gain a comprehensive understanding of their operations. This holistic insight enables organizations to make informed decisions, optimize resource allocation, streamline processes, and enhance overall operational efficiency. As a result, businesses experience improved productivity, heightened profitability, and sustainable growth prospects on a long-term basis.
Cost Savings via Inventory Optimization
When seamlessly integrated with an Enterprise Resource Planning (ERP) system, Material Requirements Planning (MRP) plays a crucial role in optimizing inventory levels. By meticulously planning the material requirements, MRP facilitates the efficient utilization of materials, thereby minimizing excess stock. This strategic approach not only helps in reducing carrying costs but also ensures that there are no shortages when fulfilling sales orders, ultimately enhancing the overall operational efficiency and cost-effectiveness of the supply chain.
Streamlined Communication and Collaboration
An integrated system plays a crucial role in breaking down silos within an organization, thereby nurturing seamless communication and collaboration among different departments. This unity not only streamlines processes but also significantly boosts overall manufacturing efficiency. Imagine the scenario where a business needs to manage integrations for separate accounting, ordering, inventory, production, and other software systems. With each update, the risk of integrations breaking and communication failures increases. However, by having your accounting, purchasing, and MRP software integrated within your ERP system from the start, you establish a robust and interconnected framework that mitigates these risks and ensures smooth operations across the board.
The Perfect Match for Custom Manufacturers
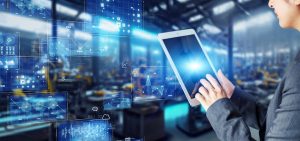
Realize the full power of ERP and MRP integration.
Make-to-order manufacturers using an integrated ERP (Enterprise Resource Planning) and MRP (Material Requirements Planning) system experience a multitude of advantages. The dynamic flexibility inherent in the integration of these systems ensures that any alterations in orders or specifications are promptly reflected in real-time updates. This seamless process not only reduces the occurrence of errors but also heightens overall customer satisfaction levels.
Accurate demand forecasting stands as a pivotal factor for custom manufacturers striving for operational excellence. Leveraging the capabilities of MRP, which can analyze historical inventory data and forecast future material requirements, facilitates proactive planning measures. When integrated within the broader ERP infrastructure, the MRP module can automatically trigger purchase orders, ensuring that inventory levels remain optimal to meet production demands promptly. This proactive approach aids in minimizing lead times, thereby enhancing on-time customer deliveries.
Effective resource allocation plays a crucial role in the operational efficiency of custom manufacturers. By implementing an integrated ERP and MRP system, companies can streamline the allocation of materials and labor, leading to reduced waste and optimized resource utilization. This meticulous approach not only enhances operational efficiencies but also contributes to cost savings and improved productivity in the long run. production costs.
The Frontier ERP and MRP Solution
Frontier ERP is a one-stop solution for high-volume, make-to-order manufacturers. A complete MRP system is one of our integrated manufacturing ERP modules. This enables companies to focus on their business expertise rather than software development and maintaining integrations.
Through its innovative design, Frontier aids in minimizing lead times by leveraging advanced production scheduling tools. Our complete system also automates materials ordering and payment processes, strengthening vendor relationships to keep up with customer demands. With just a few clicks, you can effortlessly track the status of any order at any production stage.
Conclusion
Despite the distinct difference between MRP (Material Requirements Planning) and ERP (Enterprise Resource Planning) systems, they work seamlessly together to enhance operational efficiency.
Manufacturers operating in the competitive make-to-order industry find that the combination of MRP and ERP software is crucial for their success.
As technology progresses and market demands shift, the integration of MRP and ERP solutions streamlines processes and positions manufacturers on a trajectory toward enhanced efficiency, increased profitability, and long-term sustainable growth.
Friedman Corporation helps custom manufacturers grow strategically and profitably. Contact us to learn more about our innovative solutions.