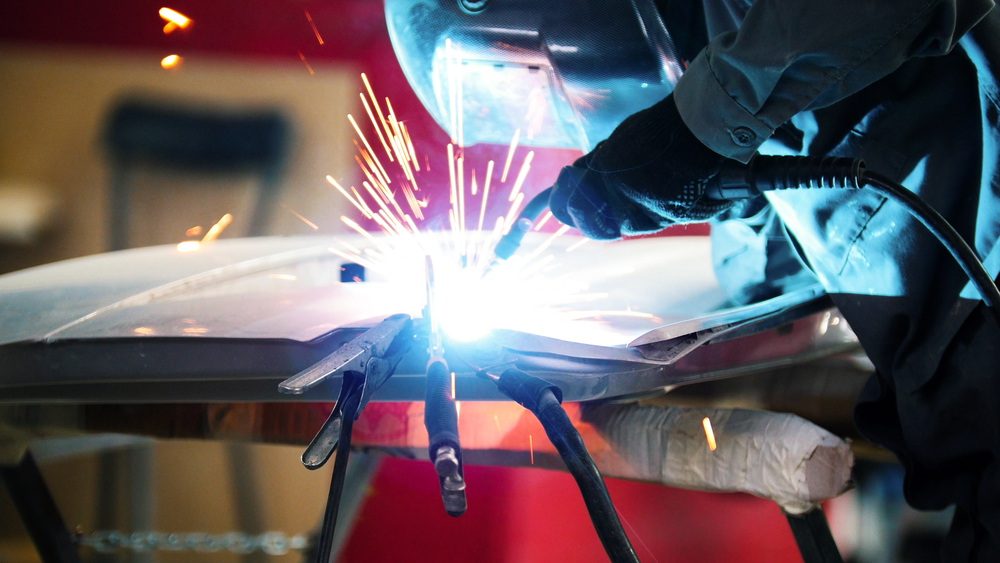
Running a steel or metal service center comes with its fair share of challenges. From managing inventory and optimizing production to maintaining quality and meeting customer demands. In this highly competitive industry, finding ways to save money without compromising on efficiency and service quality is crucial. That’s why it’s important to use software applications that can help optimize resources and streamline operations.
In this post, we will explore the benefits of ERP, CPQ, and MES systems and how embracing system integration can transform your business and significantly boost your bottom line.
Service is the Key Word in Metal Service Centers
Metal service centers provide a variety of fabrication services to their customers. Their customer base often includes custom manufacturers of garage doors, HVAC systems, office furniture, and kitchen cabinets, to name a few. From keeping an inventory of metal varieties and quick delivery to precise machine cutting and finishing processes, services vary and can become quite expensive without proper management.
Adding to that is changing market conditions, marked by evolving consumer preferences and technological advancements. This requires service centers to both diversify their current product offerings and regularly introduce innovative product lines cost-effectively. This proactive strategy demands seamless interdepartmental coordination to maintain existing product lines and efficiently implement changes and new additions.
Utilizing cutting-edge metal fabrication software like ERP, CPQ, and MES applications, can greatly enhance this coordination, enabling your company to scale smoothly in response to growth and changing demands.
What are ERP Systems?
Enterprise Resource Planning (ERP) systems are integrated software platforms used by organizations to manage core business processes. These processes include finance, sales orders, supply chain management, manufacturing, and others. With a single source of data, ERP systems eliminate data silos and enable seamless information flow across departments, improving data accuracy and enhancing overall operational efficiency. This facilitates better decision-making, strategic planning, and resource management.
ERP systems also help streamline operations by automating routine tasks and standardizing business processes. This automation reduces the need for manual intervention, minimizes errors, and accelerates processes such as order fulfillment, inventory management, and financial reporting.

Shop control with Frontier ERP’s AME manufacturing execution system can streamline your metal fabrication processes and enhance your bottom line.
ERPs play a crucial role in driving business growth and maintaining competitive advantage. The best ERP systems for manufacturing come with analytics and reporting tools that provide insights into business performance. This helps metal service centers identify areas for improvement and optimize their operations.
ERP software installation usually occurs in three ways, each with advantages. The choice is ultimately up to service center management, based on the company’s framework, budget, and desired features.
- On-Premise ERP: Installed and run on the organization’s servers and infrastructure. This provides control over the system but requires significant upfront investment and ongoing hardware maintenance.
- Cloud-Based ERP: Hosted on the vendor’s servers and accessed online. This model offers lower upfront costs, higher scalability, and remote access but may involve ongoing subscription fees.
- Hybrid ERP: Combines elements of both on-premise and cloud-based systems, offering a balance of control and flexibility.
What is CPQ Software?
Configure Price Quote (CPQ) software is a tool that streamlines the process of configuring, pricing, and quoting customizable products and services. It automates complex product configurations according to specified requirements, ensuring that the resulting combinations are valid and feasible. By integrating with systems like ERPs, CPQ software provides a seamless flow of information, from quote to order fulfillment. Integration helps maintain data consistency, reduces manual errors, and accelerates the overall sales process for your metal service center.
CPQ software enhances sales efficiency by enabling rapid and precise quote generation. It also supports dynamic pricing, taking into account factors such as market conditions, customer history, and volume discounts. Overall, CPQ software not only boosts operational efficiency, it enhances the customer experience by delivering tailored and accurate proposals quickly.
Understanding MES Software
Manufacturing Execution System (MES) software is a crucial tool that bridges the gap between enterprise-level planning systems and the physical production floor. It provides real-time monitoring, control, and optimization of production processes, ensuring that manufacturing activities are executed efficiently and accurately.
MES provides metal service centers with the ability to capture and analyze data from various stages of production. From raw material acquisition to finished product output, it provides the ability to track the entire lifecycle of production. This real-time visibility helps in identifying and addressing issues promptly, reducing downtime, and improving overall production quality and efficiency.
MES software connects with ERPs and SCMs to make operations smoother and data flow easier across the organization. This integration allows for better planning and scheduling, inventory management, and resource allocation. MES software helps metal service centers improve production performance, meet industry regulations, and satisfy customer needs through detailed insights. Overall, MES plays a vital role in enhancing operational efficiency, improving product quality, and enabling agile manufacturing practices.
Cost-Effective Metal Service Center Operations Through Integration
By combining ERP, CPQ, and MES systems in a steel and metal service center, significant cost savings can be achieved. This is done by improving efficiency, managing inventory and production better, enhancing quality control, and making more informed decisions. Integration helps your company to be more flexible, responsive, and cost-effective.
The integration allows for a variety of cost-saving measures including:
1. Improved Operational Efficiency
Streamlined Processes: Integration allows for seamless communication between ERP, CPQ, and MES systems. This reduces the need for manual data entry and minimizes errors. This results in faster completion times and lower labor costs for your metal service center, saving you money.
Real-Time Data: Real-time data is continuously shared between the three systems. This ensures that inventory levels, production schedules, and order statuses are always up to date, reducing delays.
Automated Workflow: Automation of routine tasks and workflows minimizes manual intervention. This also reduces the risk of errors and rework, saving on labor and waste costs.
2. Enhanced Inventory Management
Reduced Inventory Costs: Inventory control is one of the most crucial roles of a service center. Better visibility into inventory levels helps in maintaining optimal stock levels. This prevents your metal service center from overstocking and tying up capital. It also deters understocking situations which could lead to production delays or missed sales opportunities.
Waste Reduction: Accurate tracking and management of materials help in minimizing waste. For a steel and metal service center, this can lead to significant savings, given the high cost of raw materials. It also supports lean manufacturing principles and sustainability objectives.
Efficient Order Fulfillment: With integrated systems, inventory levels are updated in real time. This ensures that materials are available when needed, helping you meet customer demand efficiently and helping your bottom line.
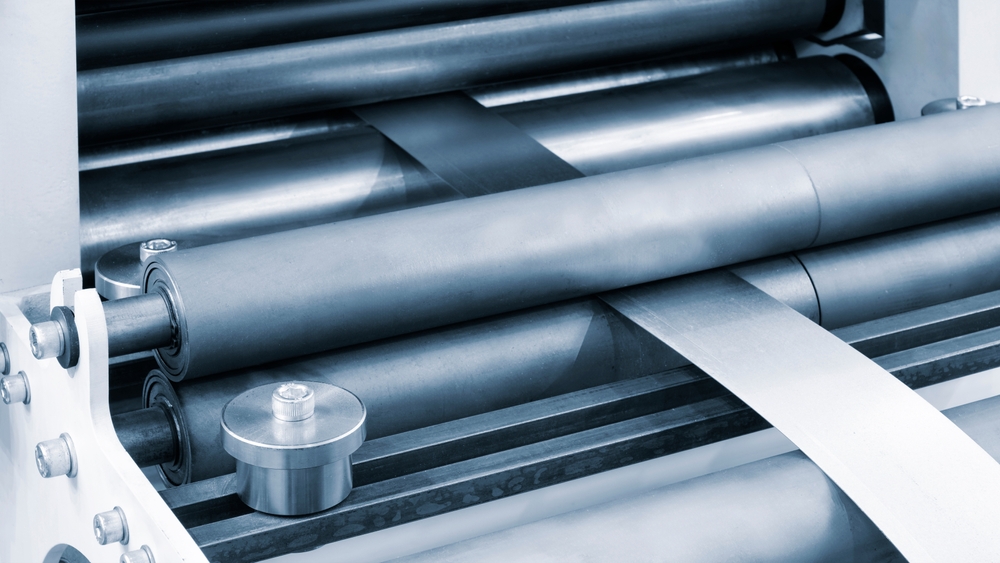
Frontier’s automated processes help your metal service center optimize production planning and scheduling, supporting your lean manufacturing principles.
3. Optimized Production Planning and Scheduling
Better Scheduling: Integration of ERP, CPQ, and MES allows for more accurate production planning and scheduling. That way resources are used efficiently and production downtime is minimized.
Precise calculations: ERP integration provides precise control over materials, unit conversions, and unique industry-specific calculations to validate distinct material characteristics.
Automated Processes: The ERP system automates processes like job scheduling and materials ordering, streamlining operations and shortening cycle times.
4. Quality Control and Reduction of Scrap
Enhanced Quality Monitoring: MES systems can provide detailed insights into the production process with robust analytical reporting, allowing for better quality control. With ERP system integration, tracking quality issues to their source allows for quick corrective actions to be taken.
Reduction in Scrap: By improving quality control, the amount of scrap and rework is reduced, leading to cost savings.
Consistent Quality: Configuration management ensures that any changes in product specifications and production processes are updated instantly, which helps in maintaining consistency and quality.
5. Enhanced Customer Satisfaction
Better Order Fulfillment: Accurate production and inventory data ensure that customer orders are fulfilled accurately and on time. This improves customer satisfaction and reduces the costs associated with order errors.
Customized Solutions: Integration can allow for better tracking of customer preferences and history. This enables your service center to offer more customized solutions and build stronger customer relationships.
3D Visualization: CPQ ERP integration allows for virtual proofs during the complex quoting process by pulling in CAD models. This ensures that the customer is getting exactly what they want and improves the customer experience. Models are also shared through the system to the shop floor, providing staff with a visual production aid.
6. Cost Reduction through Data-Driven Decision Making
Informed Decisions: Access to real-time data from both ERP and MES systems allows managers to make more informed decisions regarding production, inventory, and sales. This can lead to more strategic investments and cost-saving initiatives for your metal service center.
Performance KPIs: Data analytics can identify inefficiencies and areas for improvement, driving continuous improvement initiatives that lead to cost reductions.
Configuration Management Analytics: Analyzing configuration data helps identify patterns and trends in product and process changes, enabling proactive management and cost control.
7. Enhanced Financial Management
Accurate Cost Tracking: Integrated systems provide detailed tracking of costs associated with production, inventory, maintenance, and other operational areas. This helps in accurately calculating the cost of goods sold (COGS) and identifying cost-saving opportunities.
Cash Flow Optimization: Improved inventory management and production planning ensure that capital is not unnecessarily tied up in excess inventory, thereby optimizing cash flow.

Frontier ERP includes complete financial management features that help metal service centers reduce costs and optimize cash flow.
Profitability Analysis: Financial data integrated with operational data allows for detailed profitability analysis by product line, customer, or operational unit. This helps in identifying the most profitable areas of the business and focusing on them.
8. Reduced Administrative Costs
Automated Workflows: Workflow automation reduces the administrative burden on staff, allowing them to focus on more value-added activities rather than labor-intensive duties.
Lower Overheads: Improved efficiency and reduced errors lead to overall lower administrative overhead costs.
Documentation Management: Configuration management ensures that all changes are documented and accessible, reducing the time and effort needed for compliance and reporting.
Frontier: Your All-in-One Solution
Frontier ERP is a top-tier enterprise resource planning system tailored for discrete manufacturers and metal service centers. Whether deployed in the cloud or on-premise, it guarantees reliability and security, providing a stable yet adaptable platform. A configuration-based ERP application, Frontier offers a fully integrated suite of software modules built around a table-based, dimensional product configurator.
The built-in CPQ software automates quote and order functions, simplifying the order process for complex, customized products efficiently. Its standout feature is the advanced product configurator, which enables you to offer various product variations that are managed and produced without errors. This CPQ tool not only enhances order accuracy but also reduces manufacturing waste, ensuring a more efficient production process. Frontier’s product configurator, combined with the integrated application modules, is designed to streamline every activity involved in the order fulfillment process for both stock and fabricated metal products.
As a core component of the Frontier ERP system, our Advanced Manufacturing Execution (AME) MES is a comprehensive solution for manufacturing planning and execution. AME requires no additional system integration, streamlining implementation and usage. AME delivers real-time production schedules and job details directly to the work center in a fully paperless environment. The software provides complete data visibility, production tracking, event notifications, and detailed reporting.
Conclusion
Navigating the challenges of running a metal service center requires strategic solutions that balance efficiency and service quality without inflating costs. Integrating ERP, CPQ, and MES systems offers a transformative approach to achieving these goals.
By leveraging real-time data accessibility and automation across operations, these integrated systems streamline processes, optimizing resource allocation, reducing waste, and enhancing quality control. This not only improves operational efficiency and customer satisfaction but also empowers informed decision-making and financial management.
Embracing Frontier ERP with its robust CPQ and AME MES capabilities helps metal service centers reduce operational costs, enhance productivity, and drive profitability.
To learn more about Frontier ERP or receive a demo, contact us today!