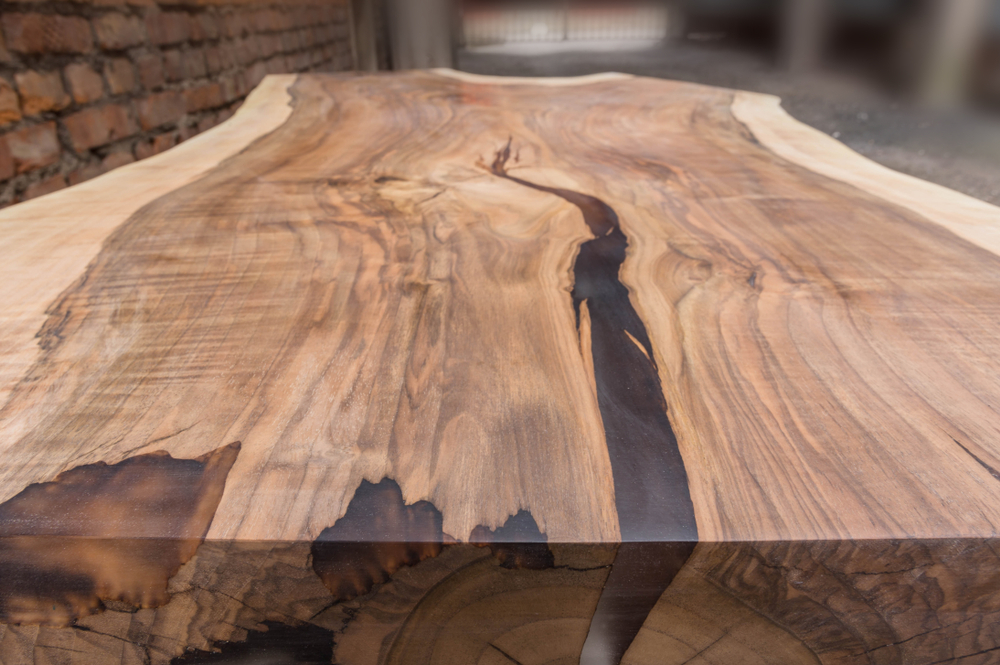
Nothing says quality like custom-crafted wood products, whether it is state-of-the-art cabinetry, ornate entry doors, or one-of-a-kind furniture. Woodworking and the manufacture of wooden products have come a long way from the days of hand tools and simple machines.
Today, modern shops use advanced woodworking design software to enhance their creative techniques. They also may use software for manufacturing and for accounting. But in many cases, these are siloed tools that are not connected. Even with a more comprehensive enterprise resource planning (ERP) system, design tools may suffer from being separate.
Through system integration, woodworking companies can take their business to the next level with more efficient processes.
What is Woodworking Design Software?
Woodworking design software helps manufacturers develop custom products for their customers. Using computer-aided design (CAD) technology, the software produces precise designs quickly, most in 3D. Different packages may also include product data and materials management features. Some of the most popular woodworking software for design are Autodesk Inventor, AutoCAD, SolidWorks, and SketchUp.
ERP: The Backbone of Your Operations
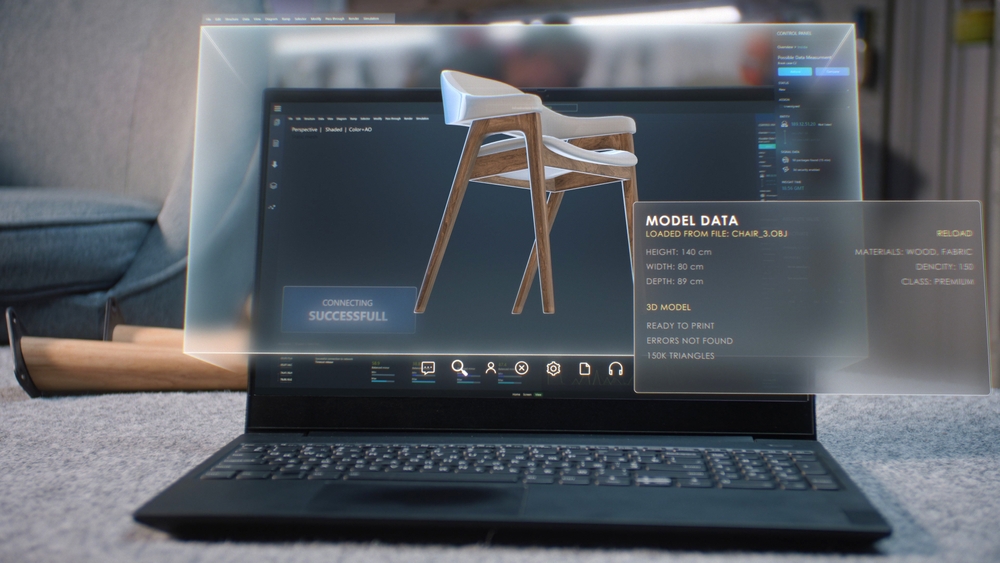
Frontier ERP integrates seamlessly with your CAD software for complete design and production efficiency.
An ERP system manages and automates essential business processes across various departments, including finance, human resources, supply chain, manufacturing, and sales. It centralizes data into a single source, eliminating silos, enabling seamless communication and real-time access to critical information. The best manufacturing ERP systems help companies streamline operations, reduce manual errors, and increase efficiency through the automation of routine tasks. Additionally, those ERPs provide robust reporting and analytics tools for informed decision-making and strategic planning.
ERP systems often include product configurators which are critical for production. Configurators allow for detailed custom options for complexly designed products like wood type, stain color, and product size. They also improve customer relations by tracking interactions and service requests, ensuring better customer satisfaction. In addition, scalable and flexible ERP systems can grow and adapt with your business’ specific needs.
Overall, ERP systems improve operational efficiency, data accuracy, and across-the-board business performance.
Woodworking Design Software and ERP Integration Advantages
Integrating your woodworking design software with an ERP system offers many advantages for your business. Let’s explore some of the key benefits:
Streamlined Data Flow
By integrating woodworking design software with an ERP, data flow becomes streamlined from initial design conception to final production. Integration eliminates the need for manual data entry and ensures seamless communication between design teams and production departments. As a result, errors are reduced, and production processes become more efficient.
Improved Accuracy and Precision
Woodworking software allows designers to create detailed 3D models of products with precision. The design software can access all data relating to the product through one source in the ERP and vice versa. This includes product configurations for each product part and component. With real-time data visibility, any changes to the product specs will reflect across the entire system immediately.
Optimized Inventory Management
ERP solutions provide real-time visibility into inventory levels and material requirements. By integrating design and ERP software, inventory records are automatically updated based on the design configurations and production orders. This ensures that inventory levels are always accurate, and materials are ordered promptly to meet production deadlines.
Efficient Production Planning
Create production schedules based on real-time demand and resource availability with ERP systems. With woodworking design software integration, configurations automatically update production plans, ensuring that the necessary resources and equipment are available when needed. This helps you meet order deadlines and maintain high levels of customer satisfaction.
Enriched Customer Experience
Perhaps one of the biggest advantages is how integration significantly enhances the customer’s experience.
The best ERP systems often include Configure, Price, Quote (CPQ) tools for the configuration and quoting process. Incorporating woodworking design software into the CPQ product configurator elevates customer interaction, offering them 3D product visualization during the design process. Customers can view a live model rendering that adjusts as configuration choices are made. This instant feedback averts potential errors but also streamlines communication among customers, dealers, and manufacturers.
Your customers can also monitor how their order is progressing in real-time. With an integrated ERP system, clients can stay informed about production progress and delivery schedules and adjust their orders effortlessly. Such transparency and adaptability greatly contribute to fostering trust for potential future sales.
Why Integrate with Frontier ERP
Frontier ERP is designed for the specific needs of make-to-order manufacturers of complex, custom products. That includes companies in the wood industry that produce items like doors, cabinetry, furniture, building products, windows, and more. Integration will greatly improve the efficiency of your operations while using Frontier ERP.
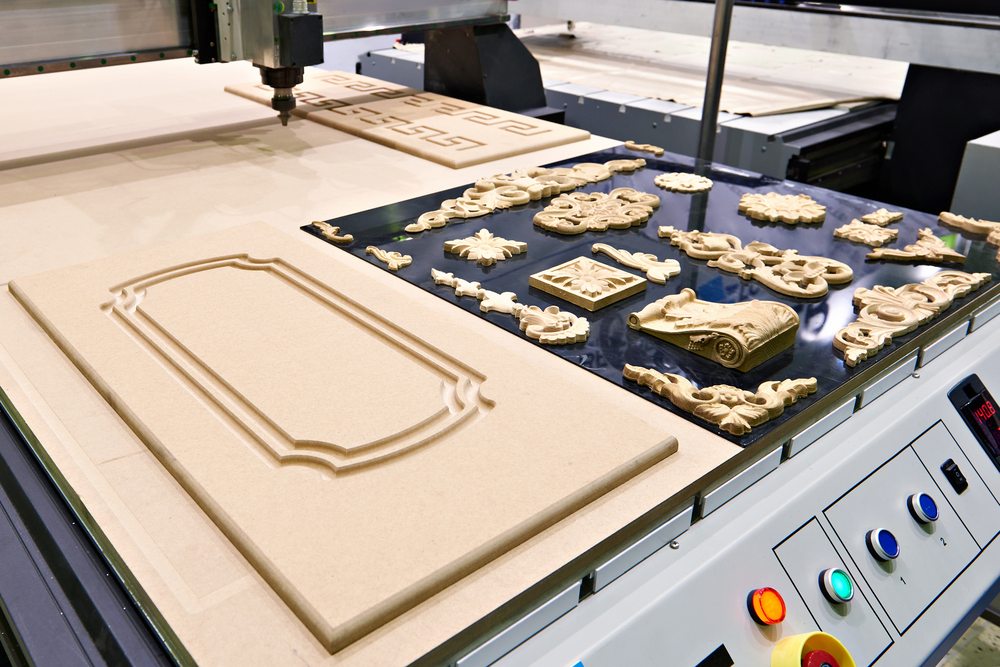
With automated production scheduling and planning, Frontier ERP allows your customer’s design ideas to come to light with precision and accuracy.
Frontier offers many features to enhance the effectiveness of your woodworking design software including:
Built-in CPQ Software
Frontier’s built-in CPQ software, which is powered by a parametric product configurator, integrates seamlessly with your woodworking design software. Integration allows for instant 3D model and drawing generation based on the configured options. Designers can then refine these models, saving time and ensuring consistency.
Frontier ERP CPQ also streamlines the sales process by automating the configuration, pricing, and quoting stages. Automation eliminates the need for manual data entry and reduces the risk of miscommunication between sales and design teams. Our CPQ ensures precise order tracking, efficient change management, and immediate communication of configurations throughout the production process. As a result, your business can increase efficiency while saving time and money.
CADFlow
Frontier CADFlow is a real game-changer for your company’s design processes. CADFlow automates the creation of your detailed 3D models, drawings, and manufacturing data for each custom order. Integrated with Frontier ERP’s parametric product configurator, this automation ensures accuracy and removes data redundancies, leading to a smoother and more efficient manufacturing process. Outputs are generated using your existing woodworking design software models and Frontier ERP CPQ product configuration rules.
But Wait, There’s More!
Frontier ERP includes many additional features to improve business operations. Including financial, sales order, and supply chain management, as well as production tracking and cut part sheets. For more details, visit our homepage.
Conclusion
By integrating woodworking design software with ERP systems, woodworking companies can significantly increase efficiency and effectiveness. Integration ensures a seamless flow of data, enhances accuracy, and optimizes planning and materials management. By automating routine tasks and improving communication across departments, integration reduces errors and delays. It also enriches the customer experience through real-time updates and precise configurations.
Frontier’s specialized features, like CADFlow and CPQ, are designed for the unique needs of the woodworking industry. In addition, seamless integration fosters a more efficient, transparent, and adaptable production process, ultimately leading to higher customer satisfaction and improved business performance. Incorporating these technologies enables your company to maintain its tradition of quality craftsmanship while leveraging modern efficiencies for business profitability and growth.
Would you like to learn more about Frontier ERP? Contact us today for a demo!