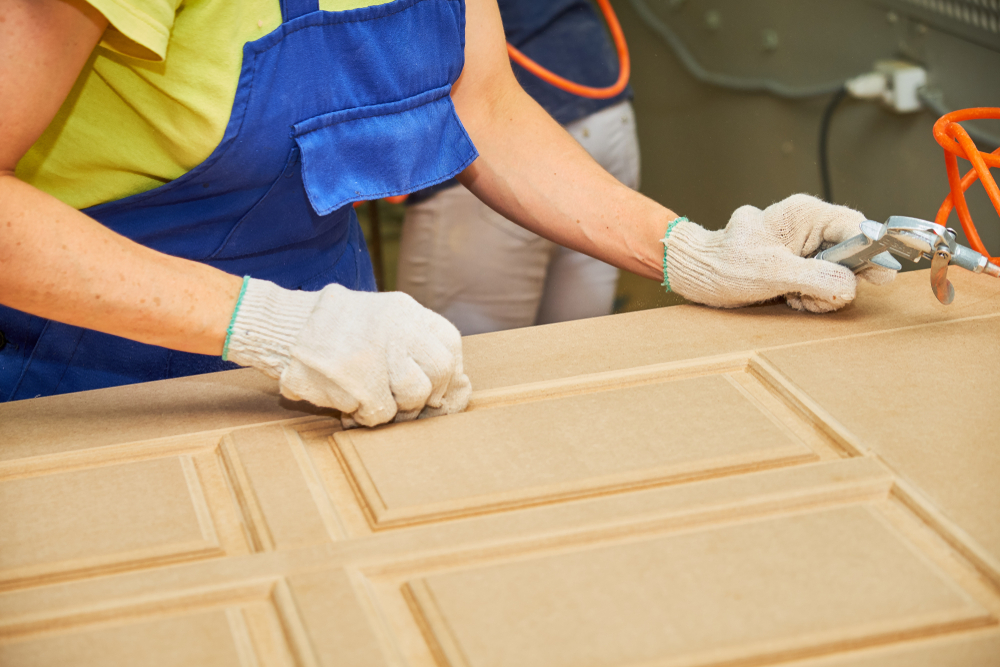
Make-to-order (MTO) manufacturers have much in common with companies that mass-produce merchandise. However, there are significant differences that are unique to MTO operations. A make-to-order manufacturing company must more closely manage complex product configurations and lead time variances. They often have more intricate cost management processes and utilize additional production methods within their custom manufacturing environment. All of these things add layers of complexity.
Customization is king, efficiency is critical, and profitability is vital in modern, MTO manufacturing. The solution? Quality ERP software with the right features to elevate your processes and optimize operations. In this post, learn more about MTO and other production methods, and how MTOs can leverage ERP software to remove stumbling blocks and streamline operations.
Understanding Make-to-Order and Other Production Methods
Manufacturing methods play a pivotal role in shaping how businesses meet customer demands, manage inventory, and optimize production processes. We would be remiss not to mention other production strategies.
Among the array of methodologies, MTO, make-to-stock (MTS), engineer-to-order (ETO), configure-to-order (CTO), and assemble-to-order (ATO) are common approaches. Each strategy offers distinct advantages and challenges that cater to various industries and product manufacturing requirements. Understanding these strategies helps businesses aiming to streamline their operations, enhance customer satisfaction, and stay competitive.
1. Make-to-Order (MTO)
In a make-to-order system, companies manufacture products only after a customer places an order based on design option variables.
- Since each product is based on specific customer requirements, MTO allows for highly customized designs and configured products.
- It requires a flexible production system that can quickly adapt to different product specifications and lead times.
- MTO manufacturing is often employed for products that have unique or highly customizable features. These may include custom-made furniture or smart blinds.
2. Make-to-Stock (MTS)
In contrast to make-to-order, make-to-stock involves producing goods in anticipation of customer demand.
- Companies manufacture products and place them in inventory before receiving customer orders.
- This strategy is suitable for products with predictable demand patterns and relatively stable production processes.
- MTS helps to reduce lead times and ensures products are readily available for use in production or for direct purchase.
- Examples include goods like school supplies or fabrics that have predictable demand.
3. Engineer-to-Order (ETO)
- Engineer-to-order products are designed and manufactured based on specific order requirements.
- Each product order is unique and typically requires engineering and design work before production can begin.
- ETO projects often involve complex, custom-made products such as machinery, industrial equipment, or infrastructure projects.
- This approach requires close collaboration between the manufacturer and the customer to ensure that the final product meets all specifications and requirements.
4. Configure-to-Order (CTO)
Configure-to-order is a hybrid approach that combines elements of both make-to-order and make-to-stock.
- Workers produce standard components and put them in inventory. Final assembly or configuration occurs only after a customer places an order.
- Customers can choose from predefined options or configurations to customize the product according to their preferences.
- CTO allows for some degree of customization while also benefiting from the efficiencies of mass production for standard components.
- Examples include glass or promotional items where customers can choose features like size and imprint.
5. Assemble-to-Order (ATO)
ATO involves producing standard components or subassemblies that are stocked for later assembly.
- Once an order is placed, the components are assembled into the final product according to customer specifications.
- ATO allows for some customization while still benefiting from the efficiency of assembling from pre-existing, stock components.
- Examples of ATO products include popular door types with glass options, semi-custom cabinets, and retail store fixtures.
MTO Incorporates Other Production Processes
MTO is a broad category that may encompass other strategies by offering varying degrees of customization and production flexibility:
- MTO often incorporates Make-to-Stock by maintaining some level of standard inventory. This is typical for commonly ordered components or materials like foam cushion cuts or dovetail drawers. This hybrid approach combines the advantages of MTO and MTS, allowing for both customization and quick order fulfillment.
- MTO incorporates Engineer-to-Order by allowing for highly customized products tailored to an individual job’s requirements. An example would be metal staircase fabrication for an industrial site.
- MTO incorporates Configure-to-Order by accommodating specific configurations or options chosen by the customer, allowing for some level of customization within a standardized framework. Varying window widths are a good example.
- MTO incorporates Assemble-to-Order by producing finished products from standardized components or sub-assemblies once an order is received. Stocking a variety of sofa legs or drawer pulls for custom cabinetry are examples. MTO with ATO provides flexibility in meeting customer demands while reducing otherwise extensive lead times.
In essence, make-to-order manufacturing is versatile enough to integrate various production strategies depending on the level of customization required. It offers flexibility to tailor products to individual customer needs while also accommodating more standardized or semi-customized offerings.
MTO Manufacturing Obstacles
Running a make-to-order manufacturing company can be challenging at the best of times. From production planning to lead time management, it’s important to identify any pain points, develop targeted strategies, and implement effective solutions. Here are some common areas where make-to-order businesses often encounter problems:
Complex Production Planning

Frontier ERP for make-to-order manufacturers removes common obstacles and helps you streamline ordering, procurement, and production processes.
Make-to-order businesses often deal with a high level of customization, making production planning more complex. Each order may require unique materials, processes, and timelines, necessitating meticulous planning and coordination.
Inventory Management
MTO companies must carefully manage their inventory to minimize excess stock. Balancing inventory levels to fulfill orders quickly can sometimes be troublesome. This is especially true when materials have long lead times for delivery.
Supply Chain Dependencies
Make-to-order businesses heavily rely on their suppliers to deliver materials and components on time. Any disruptions or delays in the supply chain can directly impact production schedules and customer satisfaction.
Lead Time Management
Managing lead times effectively is critical for MTOs to meet customer deadlines. This involves accurately estimating production times, coordinating with suppliers, and streamlining internal processes to minimize lead times without sacrificing quality.
Production Flexibility
Flexibility in production processes is vital in make-to-order manufacturing. You must be able to quickly adjust production schedules, change workflows, and adapt to new product specifications without compromising quality or efficiency.
Customer Expectations
Customers ordering MTO products typically have high expectations regarding quality, design options, and delivery times. Meeting these expectations consistently is essential for customer satisfaction and retention.
Product Costing
Product costing can be a tedious process for make-to-order manufacturers. Production process variables and the need to balance customization with profits can be frustrating. Controlling product costs while delivering unique products requires efficient resource allocation and tight cost controls.
Technology Integration
Leveraging technology is crucial for streamlining operations and enhancing efficiency for MTOs. Implementing integrated systems for order management, production scheduling, inventory control, and customer relationship management can help optimize processes and improve overall performance.
Quality Control
Quality control is essential for producing highly customized products. Implementing rigorous quality control measures throughout the production process is vital to ensure each finished product meets customer expectations.
Scalability
As an MTO company grows, it can be challenging to scale operations while maintaining flexibility and responsiveness. Investing in scalable production processes, expanding supplier networks, and adopting agile business practices can help facilitate growth without compromising efficiency or quality.
Successfully navigating these challenges requires a combination of strategic planning, operational excellence, customer focus, and continuous improvement efforts.
ERP Software Advantages for Custom Manufacturers
Enterprise Resource Planning (ERP) software can provide significant benefits for MTO manufacturers and those employing other production methods. By integrating various business processes into one centralized system, you can realize greater operational efficiency and streamlined processes. The following are just an example of Frontier ERP’s advantages.
Advanced Production Planning
Frontier ERP includes advanced manufacturing execution tools for better shop floor management. This allows custom manufacturers to create detailed production plans that consider the unique materials, processes, and timelines for each order. Frontier optimizes scheduling, resource allocation, and sequencing to ensure efficient production.
Efficient Resource Planning
ERP software helps optimize resource utilization by providing insights into inventory levels, production capacities, and resource availability. Frontier’s manufacturing management enables better resource planning to meet customer demand while minimizing costs.
Real-time Visibility and Reporting
Frontier ERP provides real-time visibility into departmental data, key performance indicators (KPIs), production status, and order tracking. Customizable reports and dashboards allow you to monitor operations, identify bottlenecks, and make informed decisions to improve operational efficiency and customer service.
Enhanced Supply Chain Management
Frontier facilitates seamless communication with suppliers and partners, enabling efficient procurement of materials and components for make-to-order production. You can track supplier performance, manage lead times, and optimize inventory levels for effective supply chain management.
Streamlined Order Management
Centralized order management processes from Frontier allow you to easily capture and process customer orders, including complex configurations. This streamlines order entry, reduces errors, and improves order fulfillment times.
Integrated Product Configuration
Many ERP systems can be connected to stand-alone configure, price, quote (CPQ) modules used to order product options, rules, and dependencies. Frontier ERP includes built-in CPQ software that utilizes our cutting-edge parametric product configurator. This allows you to manage complex configurations easily and ensure accurate production specifications.
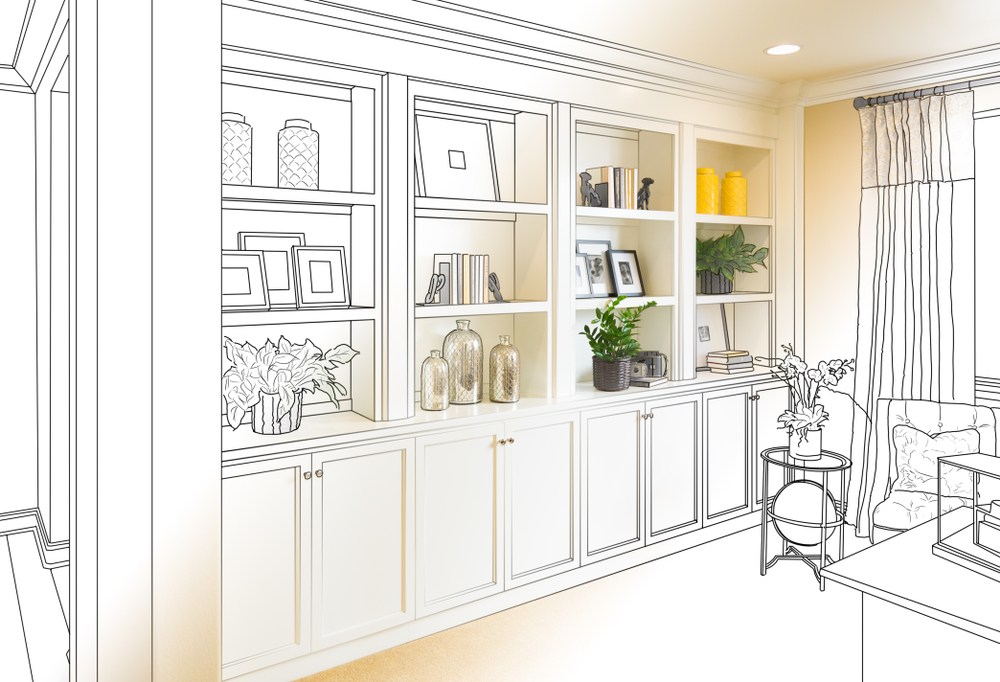
Frontier ERP includes many powerful features for make-to-order companies to streamline ordering and improve customer experience like eQuote Dealer.
Frontier also includes effortless integration with CAD design tools to support product design and engineering processes. This enables custom manufacturers to translate customer specifications into detailed product designs and production instructions, ensuring accuracy and consistency in product configuration.
Customer Relationship Management (CRM)
Frontier ERP includes CRM functionality to build stronger customer relationships and enhance satisfaction. This allows you to manage customer interactions, track order status, and provide personalized service. In addition, our dealer module can provide real-time 3D product renderings for interactive product configurations at the time customers place their orders. This improves dealer and end custom satisfaction as it reduces the likelihood of miscommunication or returns.
Optimized Cost Control and Pricing
With Frontier’s make-to-order manufacturing software, you can accurately track product costs, including materials, labor, and overhead. This enables better cost estimation for custom configurations and helps optimize pricing strategies to maintain profitability.
Seamless ERP Integration & Better User Experience
Frontier ERP integrates with your current systems and data transfer services to maintain data integrity. DataBroker and our other ERP data migration solutions remove common ordering roadblocks for increased efficiency. Frontier also has a user-friendly interface that enables MTOs to minimize training time to save money.
Quality Management
ERP software modules all support quality management that allows you to define quality standards. Our manufacturing ERP takes quality control to the next level with inspection tracking and conformance management. This ensures that each configured product meets the required quality standards before delivery to the customer.
Scalability and Flexibility
Frontier ERP grows with your business, allowing you to add new users, expand functionality, and support growing transaction volumes. This flexibility ensures that your ERP system can adapt to changing business needs and accommodate future growth.
Conclusion
Make-to-order businesses face many unique operational challenges like advanced production planning and complex product configurations. By leveraging the best ERP for manufacturing, your make-to-order business can streamline operations, improve efficiency, enhance customer satisfaction, and ultimately drive profitability.
Consider the robust functionality of Frontier ERP and our MTO industry expertise to enhance your operations and improve your production efficiency. Contact us today to learn more.
Key Takeaways
Unique Challenges of Make-to-Order Manufacturing: Make-to-order (MTO) manufacturing presents distinct challenges. These include complex production planning, inventory management, and supply chain dependencies due to its focus on customization and flexibility.
ERP Solutions Address Specific Needs: Enterprise Resource Planning (ERP) software offers tailored solutions to address challenges faced by MTO manufacturers. It provides features like advanced production planning, efficient resource utilization, and real-time visibility.
Comprehensive Functionality: ERP systems for manufacturing like Frontier ERP offer a wide range of functionalities, including streamlined order management, integrated product configuration, and enhanced supply chain management to optimize MTO operations.
Business Benefits Beyond Efficiency: The best manufacturing ERP software not only improves operational efficiency but also facilitates better cost control, adherence to quality standards, and scalability to support business growth.
Frontier is a Powerful Make-to-Order Manufacturing Software Solution: Frontier ERP stands out as a robust solution for MTO manufacturers, providing the necessary tools and features to navigate the complexities of custom manufacturing for efficient business operations.