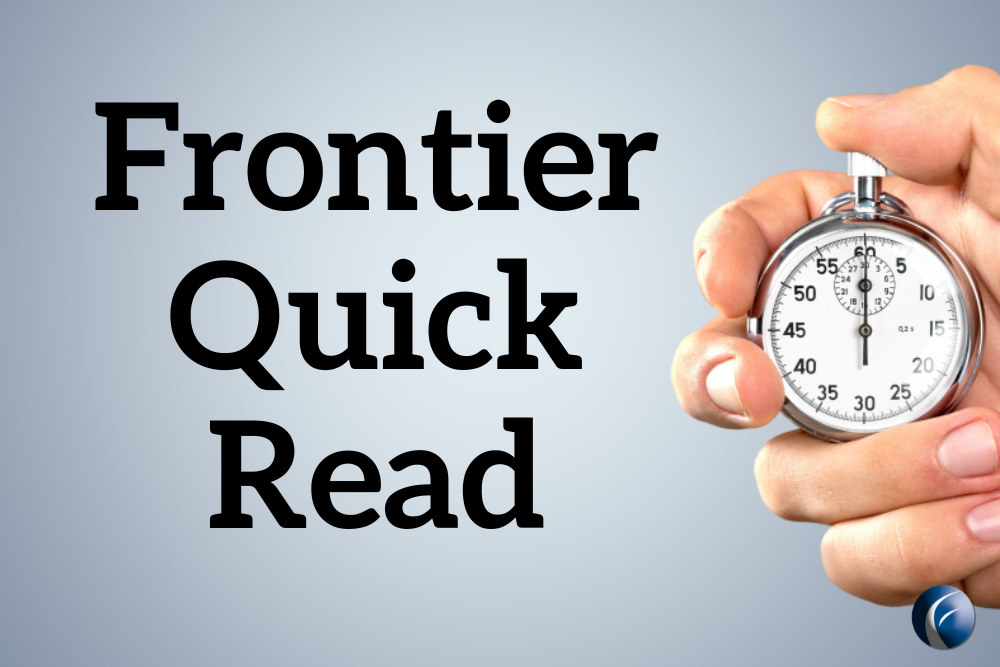
As the end of the year approaches, manufacturers face the often-daunting task of conducting a year-end inventory. This process can be stressful, time-consuming, and prone to errors. However, with IBM ERP by Frontier, manufacturers can simplify their inventory management, save time, and ensure accuracy in their year-end counts.
Let’s explore how Frontier ERP can make your year-end inventory hassle-free.
Inventory Day Customer Communication
It’s important to communicate clearly with customers before and during year-end inventory. Frontier can help with customer communications about potential delays or changes in order fulfillment. The system can automatically send notifications to customers regarding inventory activities, shipping schedules, and any impacts on delivery times.
For example, if inventory day affects shipping schedules, you can use ERP alerts to notify customers early. In addition, if your customer portals integrate with Frontier’s IBM ERP, customers can track their orders and make changes as needed.
Effective customer communication helps manage expectations and strengthens customer relationships by demonstrating transparency and professionalism.
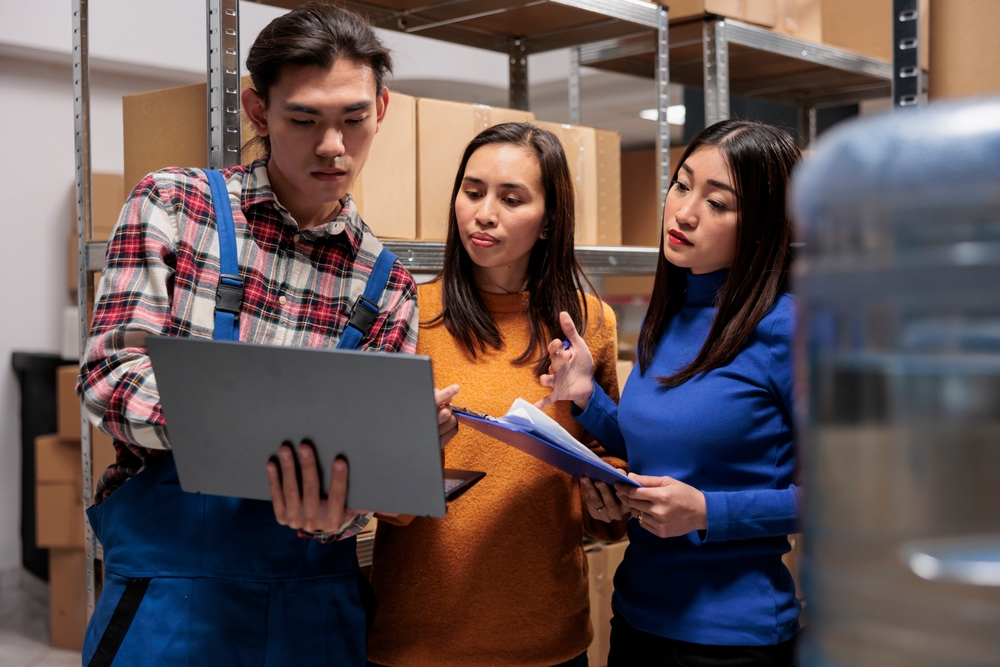
Streamline your year-end inventory with the powerful features of Frontier IBM ERP.
Streamlined Year-End Inventory Tracking
One of the most challenging parts of the year-end inventory process is tracking all items accurately. When stock is constantly being received, sold, or moved between locations, it can be difficult to keep track of every change. Frontier’s IBM ERP software includes an integrated inventory management system that provides real-time updates on stock levels at all locations.
With Frontier, each transaction automatically updates inventory records including purchases, sales, or internal transfers. Real-time tracking means that at any given moment, your inventory levels are accurate and up-to-date. This reduces the chances of discrepancies when performing your year-end counts.
There is no need to rely on manual counts or old data with Frontier. You can easily check the ERP system for exact stock levels. It shows you where items are located and which ones are low or overstocked. This makes year-end inventory less likely to have errors and provides a clear view of your resources as you finish the year.
Integrated IBM ERP Accounting Functions
An essential part of conducting year-end inventory is linking stock counts with financial records. Updating both inventory and financial systems by hand causes duplicate work, errors, or mismatches. Frontier ERP solves this problem by seamlessly integrating accounting functions with inventory management.
Integration means that when you update your inventory, financial information like inventory valuation and cost of goods sold (COGS) is automatically updated too. This eliminates manual data entry and ensures that your financial statements are always in sync with physical stock levels.
For year-end reporting, integration also provides an accurate snapshot of your business’s financial health. Additionally, you gain more visibility into how your stock levels impact profitability, allowing you to make more informed decisions going forward.
Error Reduction With Barcode Scanning
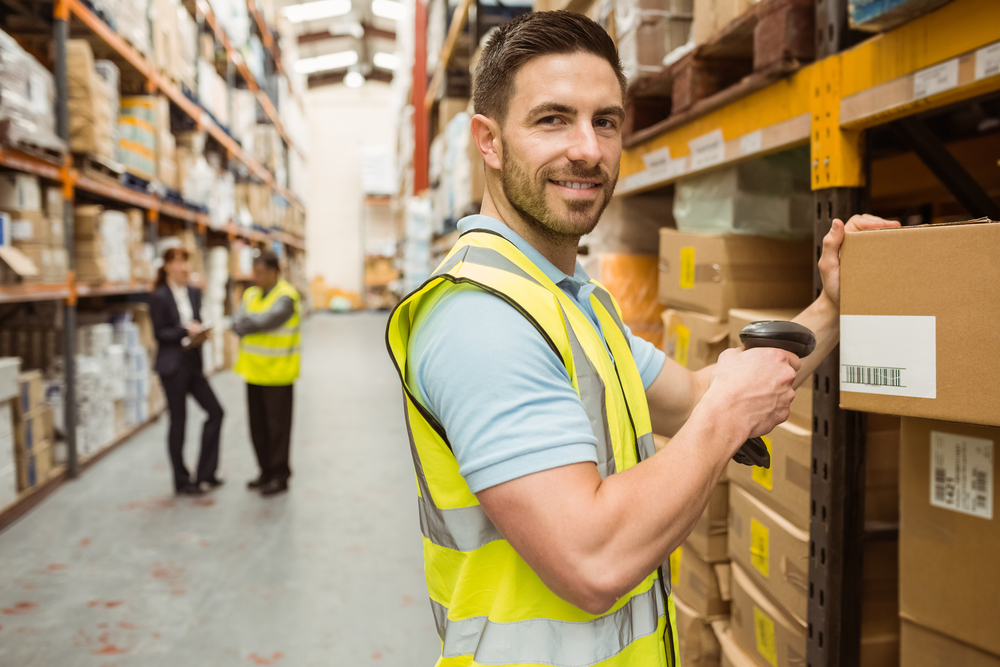
Using barcode scanning during your physical inventory can make the process faster and your counts more accurate.
As mentioned previously, manual data entry is always a source of potential errors in inventory counts. Miscounting items or entering incorrect quantities can easily happen. During the year-end process, the pressure to count and update stock quickly can increase the chances of mistakes as well. As one of the best manufacturing ERPs, Frontier supports barcode scanning, significantly reducing these types of errors.
By using barcode scanners, inventory can be updated quickly and accurately. Since each item is scanned when received, shipped, or transferred, all system data is exact. Powered by IBM, Frontier generates alerts for missing or unscanned items and creates audit trails for tracking inventory movements. This improves accuracy, reduces the need for manual input, and speeds up the year-end inventory process.
Barcode scanning also helps streamline the physical counting process. Instead of manually logging each item, employees can simply scan the barcode and the system does the rest. This leads to faster, more accurate counts, with fewer chances of human error.
Real-time Data Synchronization
In manufacturing businesses without ERP systems, different departments frequently work in data silos. Sales, production, inventory, and accounting work with separate systems or data that aren’t always in sync. This can lead to confusion, mistakes, and inefficiencies during year-end inventory. Frontier’s IBM ERP eliminates this issue by synchronizing data across all departments in real time.
As one of the best ERP programs, Frontier connects every department seamlessly. This ensures that everyone uses the same information, and no one needs to use outdated or incorrect data. For example, once a sales order is processed, the ERP system adjusts inventory levels immediately. This ensures that all departments access the proper inventory count verification or appropriate reports. Whether it’s checking stock levels or reviewing year-end financials, miscommunication or discrepancies between departments are reduced with Frontier.
Automated, Precise Reporting
Manual reporting can be a nightmare during year-end inventory. Gathering data, creating reports, and analyzing inventory levels by hand is a pain. Not only is it time-consuming but it also increases the likelihood of errors. You can access automatically generated detail reports in just a few clicks with Frontier ERP.
These reports include everything you need for year-end analysis. Details include stock levels, discrepancies, order history, and even alerts for items that are approaching their reorder points. By automating this process, the ERP system saves you valuable time and ensures that reports are comprehensive and accurate. Whether you need high-level overviews or granular, item-by-item reports, automated functions streamline the entire reporting process.
Additionally, the IBM-backed ERP system offers customizable reporting options. This allows you to tailor reports to meet your specific business needs. Automated reports also help detect any inventory calculation issues early on. That way you can address them before finalizing your counts and reduce the risk of errors when your year-end numbers are finalized.
Efficient Stock Valuation
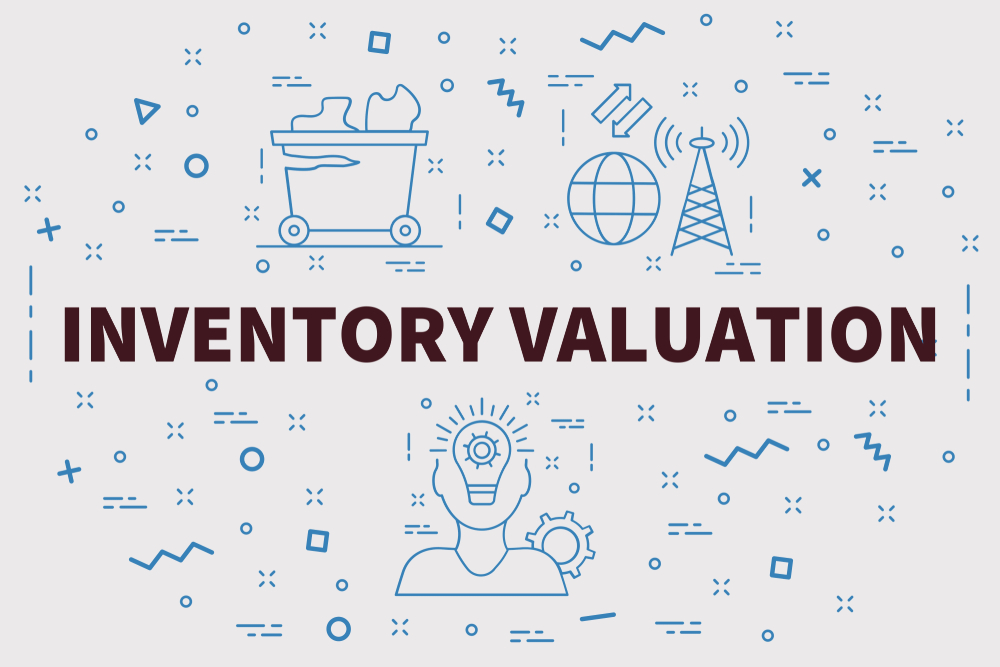
With a centralized database that updates records instantly, your year-end inventory valuation will be a breeze with Frontier ERP.
Year-end inventory is not just about counting physical stock. It’s also about determining the value of that stock for financial reporting. Traditionally, calculating stock values at year-end involves complex manual calculations. Plus adjustments based on market value fluctuations, and spoilage must be taken into consideration.
Frontier ERP helps you quickly calculate the COGS based on the cost of raw materials, labor, and overhead. This count updates automatically as inventory transactions are processed, so manufacturers always know the current stock value. The IBM ERP system supports different valuation methods like FIFO, LIFO, and average cost. This gives you flexibility in managing and reporting stock valuation.
By automating stock valuation, Frontier reduces the complexity of the year-end process and ensures accurate financial statements. By knowing that inventory counts align with physical stock and financial records, you can close your books with confidence.
Forecasting and Planning for the New Year
Most companies wrap up the current year with physical inventory counts. It’s also an opportunity to prepare for the year ahead. IBM ERP by Frontier helps manufacturers forecast future demand by analyzing historical data. It can suggest optimal stock levels and help you plan purchase orders to ensure a smooth new year.
By using historical trends, Frontier ERP provides you with insights into future shifts in demand. This allows you to adjust your purchasing strategies, production timelines, and inventory levels before the new year even begins. This proactive approach ensures that you are better prepared to meet customer demand and avoid stockouts in the new year.
More About Frontier IBM ERP
Frontier is one of the best ERP programs for high-volume, custom manufacturers. It is designed for the IBM i Power platform, which was once called AS 400 and i Series. As an IBM Silver Business Partner, we work closely with the IBM i development team. This helps keep Frontier well-suited for the IBM i operating system. Frontier can be deployed on-site, in the cloud, or as a hybrid.
You can still use Frontier ERP on a platform different from IBM. While Frontier uses IBM I on the backend, our web-based GUI is platform-agnostic. That way, we can offer all manufacturers powerful ERP tools and flexibility.
Don’t Miss Our Live Webinar!
Register Now!
Want to learn how to tackle those daunting year-end tasks in a snap? This is your chance to learn how to use Frontier ERP for a smooth year-end transition. If you can’t attend, register anyway and we’ll send you the webinar recording link that includes all of the valuable information.
If you have additional questions about how Frontier ERP can make your year-end inventory easier, let us know!