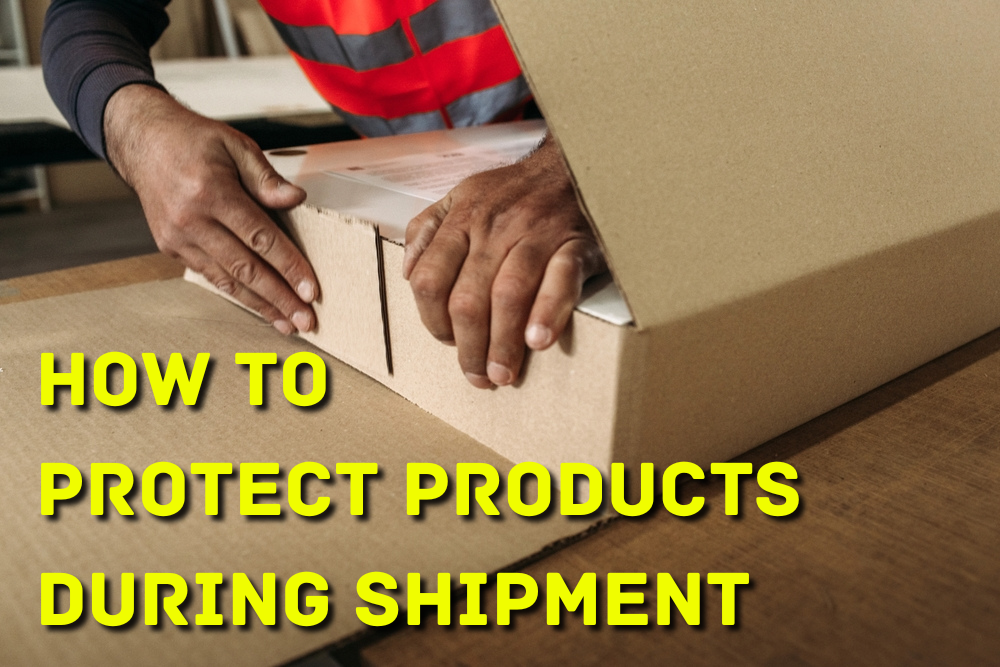
The dreaded words “package damaged in transit” are enough to send a wave of concern through any manufacturer, especially those who specialize in custom, make-to-order products. Beyond the immediate frustration of dealing with an unhappy customer, the financial impact can be significant, as replacement costs for bespoke items often far exceed those of standard products. They cannot simply pull a replacement product from a shelf to replace the client’s order. Items must be reworked or recreated, unlike mass-produced products.
In this blog post, we’ll explore the common causes of shipping damage and provide practical tips on how to reduce these risks, protect your products, and control packaging and shipping costs.
Common Problems That Lead Damaged Packages
Custom manufacturers often face several common challenges when trying to protect their products from damage during shipping. Any product can be damaged; from doors and windows to cabinets and blinds. These issues can lead to financial losses, customer dissatisfaction, and logistical complications. Here are some of the key problems:
Inadequate Packaging | Insufficient or inappropriate packaging materials can lead to a package damaged in transit. Packaging that is not tailored to the product's specific needs can fail to protect it adequately. Products may be crushed, scratched, or otherwise damaged, leading to customer complaints, returns, replacements, and extra shipping costs. |
Environmental Factors | Products can be exposed to varying environmental conditions (e.g., temperature, humidity, moisture) during shipping. Products sensitive to environmental factors may warp, rust, or become discolored if not properly protected. |
Handling Mishaps | Rough handling by carriers or during loading/unloading can lead to physical product damage. Even well-packaged items can be damaged if they are dropped, thrown, or mishandled. |
Insufficient Cushioning | Lack of adequate cushioning materials (e.g., bubble wrap, foam) can lead to package damage in transit. Items that are not properly cushioned can suffer from vibrations or shocks, especially during long-distance transportation. |
Improper Labeling | Inadequate or unclear labeling (e.g., "Fragile," "This Side Up") can result in improper handling. Products may be placed upside down, stacked incorrectly, or handled roughly, increasing the risk of damage. |
Incorrect Palletizing | Poor palletizing practices, such as overstacking or using damaged pallets, can cause instability during shipping. Stacked pallets can collapse, leading to product damage and possible safety hazards. |
Cost Constraints | Budget limitations may force manufacturers to use lower-quality packaging materials or cut corners in protection measures. Some cost-saving measures can increase the risk of product damage and result in higher long-term costs from returns and replacements. |
Lack of Package Testing | Inadequate testing of packaging designs for real-world shipping conditions can leave vulnerabilities undiscovered. Packaging might fail during actual transportation, leading to unforeseen damage to products |
Addressing these challenges requires careful planning, proper material selection, and thorough testing of packaging solutions to ensure products arrive safely at their destination.
Protecting the Products
Protecting your custom products from shipping damage is crucial for ensuring they arrive safely and maintaining customer satisfaction. Here are some strategies and best practices that you can use to protect your products during shipping:
1. Use Quality Packaging Materials
- Choose the Right Materials: Select packaging materials that match the product’s size, weight, and fragility. Some options include corrugated cardboard boxes, bubble wrap, foam inserts, and air pillows.
- Multi-Layer Packaging: Use multiple layers of protection, such as an outer box, padding, and an inner box, to absorb shocks and vibrations.
2. Design Custom Packaging
- Tailored Fit: Design packaging that fits the product snugly, minimizing movement inside the box or framework. Custom inserts or molded foam can keep products securely in place.
- Product-Specific Solutions: For irregularly shaped or delicate items, consider custom packaging solutions that provide optimal protection.
3. Apply Proper Cushioning
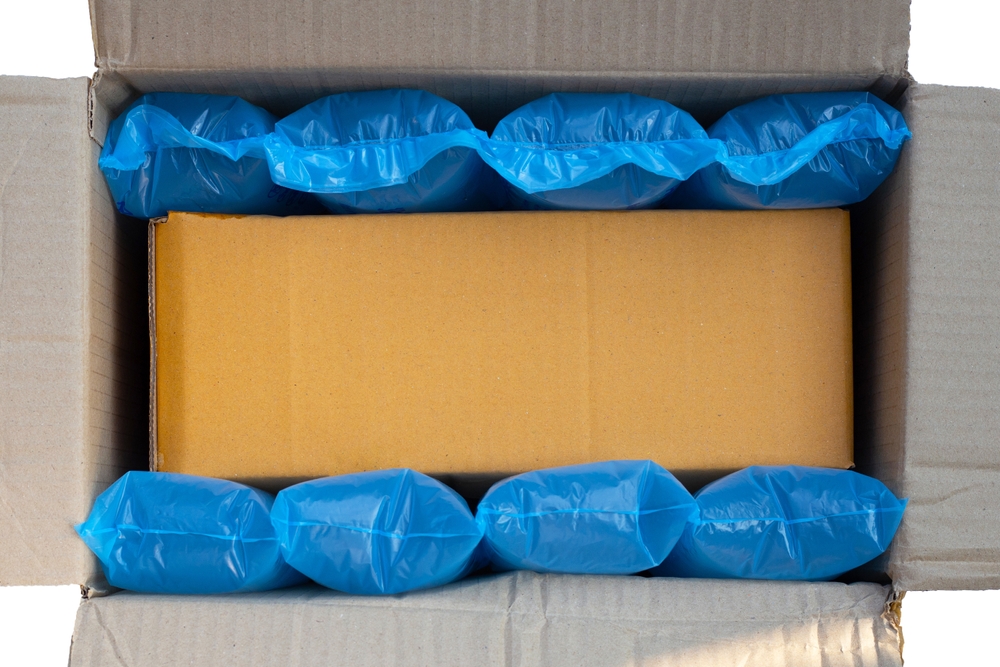
Proper cushioning and inner boxes can prevent product movement that can result in a package being damaged in transit.
- Impact Absorption: Use cushioning materials like foam, bubble wrap, or air cushions to protect against impacts and vibrations.
- Void Fillers: Fill empty spaces within the package to prevent the product from shifting during transit.
4. Ensure Proper Sealing
- Secure Sealing: Use strong packing tape or adhesive to seal packages securely to avoid having a package damaged in transit. Ensure all seams and edges are reinforced to prevent the package from opening during shipping.
- Tamper-Evident Seals: Consider using tamper-evident seals to deter and detect unauthorized access.
5. Label Packages Clearly
- Fragile Items: Clearly label fragile items with appropriate stickers, such as “Fragile,” “Handle with Care,” or “This Side Up,” to alert handlers.
- Special Instructions: Include any necessary handling instructions, such as temperature or humidity requirements.
6. Use Palletizing Techniques
- Proper Stacking: Stack products on pallets or in LTL boxes evenly and securely to prevent package damage in transit.
- Shrink Wrapping: Wrap pallets with stretch film or shrink wrap to stabilize the load and protect against dust, moisture, and tampering.
- Strapping: Use strapping or banding to secure products on pallets, particularly for heavy or bulky items.
7. Consider Environmental Protection
- Environmental Control: For sensitive products, use UV-protection packaging or temperature-controlled shipping options.
- Moisture Protection: Protect products from moisture by using desiccants, waterproof packaging, or plastic liners inside boxes.
8. Test Packaging Designs
- Simulate Shipping Tests: Conduct drop tests, vibration tests, and compression tests to ensure packaging can withstand the rigors of shipping.
- Continuous Improvement: Regularly review and improve packaging designs based on test results and feedback from shipping experiences.
9. Use Appropriate Shipping Methods
- Select Reliable Carriers: Choose shipping carriers known for their careful handling and reliability to avoid having a package damaged in transit.
- Expedited Shipping: For fragile or high-value items, consider using expedited shipping options that minimize handling and transit time.
10. Educate and Train Staff
- Packaging Training: Train employees on proper packaging techniques and the importance of following product packaging guidelines.
- Handling Training: Ensure all staff involved in the shipping process are trained on the correct handling procedures to minimize the risk of damage.
11. Leverage Technology
- Shock and Tilt Indicators: Use devices that monitor and record shock, tilt, or temperature conditions during transit. These indicators can help identify and address potential issues.
- Smart Packaging: Consider using IoT-enabled packaging that provides real-time data on the condition of the product during shipping.
Manufacturers can lower the chances of having packages damaged in transit by using these strategies. This leads to happier customers and saves money on returns and replacements.
Package Damaged in Transit? Now What?
If a package is damaged in transit, you can take several steps to address the situation, minimize losses, and prevent future occurrences. Here’s what a manufacturer can do:
Document the Damage
When a package is damaged in transit, the first step is to document the damage thoroughly. If the customer finds damage, ask for photos and descriptions of the damaged items right away. If damage is found during an inspection before delivery, take photos, write detailed descriptions of the damage, and include relevant shipping information. This documentation serves as the foundation for any claims or further action.
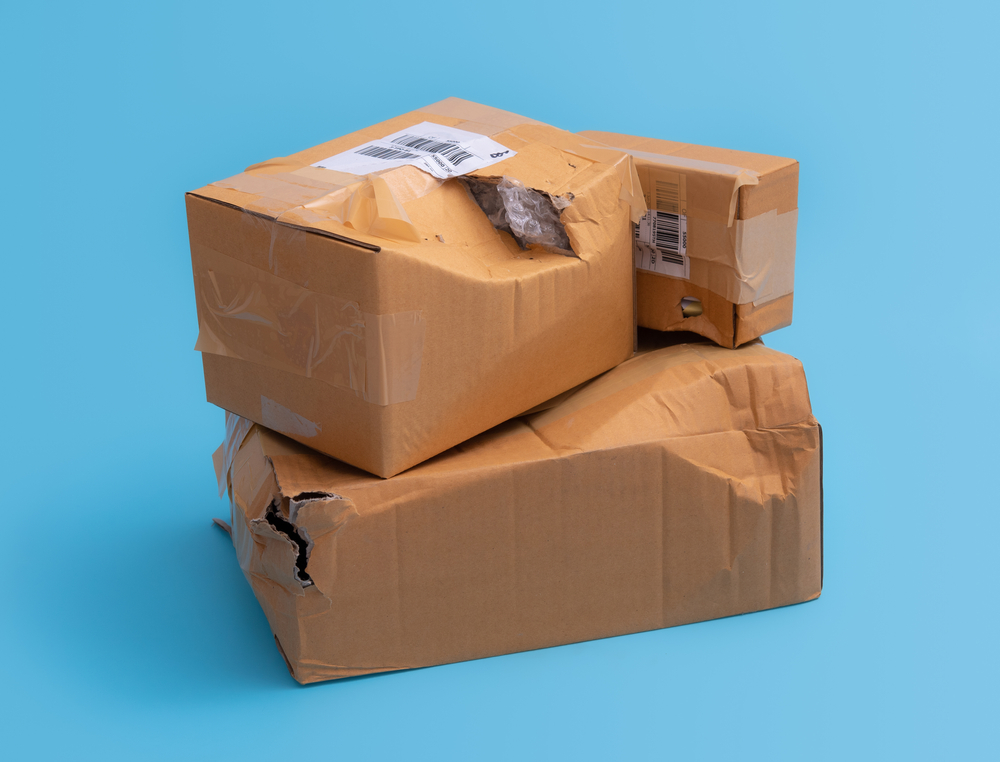
Clear customer communication is key to successful resolution when they have received a package damaged in transit.
Assess the Extent of the Damage
After documenting the damage, the next step is to assess its extent. The manufacturer should evaluate whether the damage is minor or if it significantly affects the product’s functionality or value. Additionally, inspecting the condition of the packaging materials can provide insight into how the damage occurred.
File a Claim with the Shipping Carrier
If the damage occurred during shipping, the manufacturer should promptly file a damage claim with the shipping carrier. Most carriers have specific procedures and timeframes for reporting damage, so it’s crucial to act quickly. The claim should include all necessary documentation, such as photos, descriptions, and proof of the product’s value or associated costs. Properly filing a claim can help recover losses associated with the damaged shipment.
Communicate with the Customer
Open and prompt communication with the customer is essential after discovering a package damaged in transit. You should acknowledge the issue, apologize for the inconvenience, and offer potential solutions. Solutions may include conducting a field service call, sending a replacement product, providing a refund, or offering a discount on future purchases. Clear communication helps maintain customer trust and satisfaction.
Replace or Repair the Product
Depending on the extent of the damage, you may need to replace or repair the product. If the product is beyond repair, a replacement should be sent to the customer as quickly as possible. This could take quite a bit of time for some custom-manufactured pieces. If it can be repaired, perform the repair and cover the shipping costs for returning the damaged item. This approach ensures that the customer receives a functional product promptly.
Improve Packaging and Shipping Processes
After fixing the problem, check how similar products are packaged and shipped to avoid future damage. This may involve analyzing the incident to determine if changes to packaging materials or design are necessary. If the package damaged in transit was caused by mishandling or poor packaging, you should improve their packaging and shipping procedures. Providing feedback to packaging suppliers or carriers can also help improve the quality of materials and handling.
Implement Preventative Measures
To further reduce the risk of future damage, implement preventative measures. Enhancing quality control checks for packaging before shipment can ensure that all products are adequately protected. Consider using a different shipping company to lower the risk of damage.
Review Customer Policies
Manufacturers should regularly review their customer-facing policies, particularly return and refund policies. They should clearly outline the process for reporting damaged goods and requesting replacements or refunds. If applicable, warranty terms should also be reviewed to ensure that they cover goods damaged in transit. Clear, fair policies can help manage customer expectations and resolve issues more efficiently.
Collect Customer Feedback
After resolving the issue, manufacturers should seek feedback from the customer on how the situation was handled. This feedback can provide valuable insights into customer satisfaction and highlight areas for improvement. Tracking customer satisfaction levels over time helps ensure that the resolution process meets or exceeds customer expectations. This is key to maintaining strong customer relationships.
Packaging Procurement: Balancing Cost and Quality
Packaging procurement plays a critical role in the manufacturing and distribution process. It directly impacts both the protection of products and the company’s bottom line. It is important to find the right balance between cost and quality. Products need to reach customers in good condition while the company remains profitable.
Effective packaging procurement involves selecting materials that are durable, reliable, and tailored to protect the product. Additionally, manufacturers must consider factors such as supplier reliability, lead times, and overall supply chain efficiency. By optimizing packaging procurement, companies can reduce waste and minimize package damage in transit, all while controlling costs.
Sustainability in Packaging: A Growing Priority
Sustainability has become a crucial consideration in packaging procurement, as consumers and businesses alike are increasingly prioritizing eco-friendly practices. Manufacturers are now looking for packaging solutions that not only protect their products but also minimize environmental impact. This shift towards sustainable packaging involves choosing materials that are recyclable, biodegradable, or made from renewable resources.
In a Packaging Dive article, Benjamin Trent, managing consultant at Smithers stated, “Sustainability in e-commerce [packaging] really has become an imperative. It’s no longer a nice-to-have,” he said. “Why? Because damaged product is the least sustainable option. In fact, half of consumers have noted that they will stop ordering, or order less frequently, if they receive a damaged product.”
Companies are adopting innovative designs that reduce material usage without compromising protection, such as lightweight packaging and minimalistic designs. Emphasizing sustainability in packaging not only helps reduce a company’s carbon footprint but also appeals to environmentally conscious consumers, enhancing brand reputation and customer loyalty. In the long term, investing in sustainable packaging can lead to cost savings through reduced waste and improved efficiency in the supply chain.
ERP Systems and Packaging Cost Management
An Enterprise Resource Planning (ERP) system is a powerful tool for manufacturers aiming to keep packaging costs in check. By integrating various business processes into a single, unified platform, an ERP system provides comprehensive visibility into sales, product configurations, procurement, inventory, and production. This visibility allows manufacturers to track orders, raw materials, and packaging material usage in real time, identify inefficiencies, and avoid overstocking or stockouts.
With accurate demand forecasting and inventory management capabilities, an ERP system helps ensure that packaging materials are ordered in the right quantities at the right time, reducing waste and minimizing the costs associated with excess inventory or last-minute purchases. Additionally, by automating procurement workflows, ERP systems streamline supplier management and facilitate better negotiations for bulk purchases, further driving down packaging costs.
Optimizing Packaging Processes with ERP Analytics
Beyond cost management, an ERP system offers advanced analytics tools that enable manufacturers to continuously optimize their packaging processes. These tools can analyze data on packaging material performance, costs, and supplier reliability. This provides insights that help manufacturers make informed decisions about which materials and suppliers to use. By leveraging this data, companies can identify cost-saving opportunities, such as switching to more cost-effective or sustainable materials without compromising quality.
ERP systems also help you track and analyze packaging costs for different products and regions. This makes it easier to find areas where you can reduce expenses and ensure your packaging solutions are efficient and effective.
Frontier ERP and Varsity Logistics: The Perfect Partnership
Frontier ERP is the leading choice in ERP systems for custom manufacturers on an IBM platform. Whether you choose on-premise deployment or cloud hosting, our ERP software is optimized for the IBM i Power platform (AS/400, i Series ERP).
Frontier integrates seamlessly with our logistics partner, Varsity Logistics to help with shipping and distribution needs. Varsity’s multi-carrier shipping software seamlessly connects with your Frontier ERP, ensuring smooth data flow and eliminating the need for multiple platforms. The integration allows you to:
- Manage Suppliers Effectively
- Generate Robust Analytics and Reports
- Eliminate duplicate data entry
- Real-time visibility at every stage
- Control costs with ease
- Deliver a frictionless customer experience
- Choose the best carrier
Conclusion
Minimizing the risk of having a package damaged in transit is crucial for both cost control and maintaining customer satisfaction, especially for custom manufacturers. By addressing common shipping challenges, investing in quality packaging, and leveraging software solutions like Frontier and Varsity Logistics, manufacturers can significantly reduce damage risks, lower costs, and streamline their shipping processes.
Implementing these best practices not only helps protect your products but also strengthens your customer relationships and enhances your bottom line. Don’t let transit damage erode your profits—take proactive steps to safeguard your shipments and ensure successful deliveries every time.
Contact us today to learn more about the great benefits Frontier and Varsity can bring to your company!