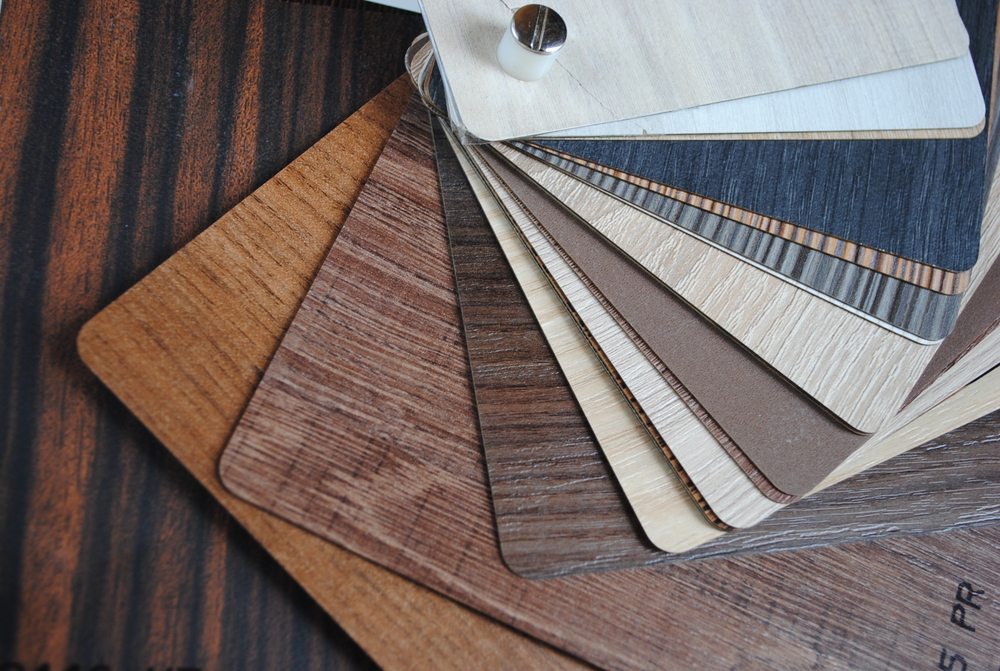
In today’s rapidly evolving furniture industry, the demand for customized furniture solutions is on the rise. This trend has led to the adoption of technology to improve operations and enhance efficiency. This article explores furniture industry trends, the benefits of ERP and CPQ software for furniture manufacturing, and ways to enhance business operations.
Trends in Furniture Manufacturing
The furniture industry continues to evolve to meet changing consumer preferences and technological advancements. Here are some notable trends:
Sustainable Furniture:
At the forefront of furniture manufacturing is the inclusion of sustainable materials, with more companies adopting eco-friendly materials and sustainable production methods. This aligns with the growing demand for environmentally responsible products and reflects a broader societal shift towards sustainability.
Office Furniture Trends for Remote Work:
More people working from home means more need for comfortable and flexible home office furniture. Some employees are back in the office, but many still work from home and need furniture for remote work.
Retail Product Display Furniture:
Retailers are increasingly investing in custom display furniture to create unique and engaging shopping experiences to draw more customers. These aesthetically pleasing and adaptable displays are essential for enhancing brand identity and customer engagement.
Advancements in ERP Systems:
ERP integration systems are becoming more sophisticated, offering features like real-time data analytics. This data-driven approach empowers manufacturers to make informed decisions, improving overall efficiency and decision-making.
CPQ Software Innovations:
CPQ software is always improving, with better interfaces and more options for customizing furniture for offices, stores, or homes. The latest innovations in CPQ software for furniture manufacturing provide an even more personalized, efficient, and seamless buying experience. This is particularly true for CPQ tools as part of a resource planning ERP system.
How CPQ Software for Furniture Manufacturing Works
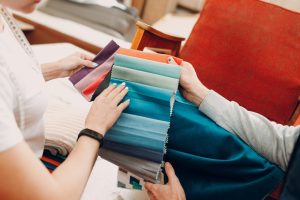
CPQ in ERP software for furniture manufacturing enables clients to customize and get accurate pricing at the time of order.
Customers more often want furniture that meets their individual needs. That’s why furniture manufacturers should consider using CPQ tools as part of their ERP software for furniture manufacturing. A robust product configurator lets customers easily choose different custom order options like material, size, color, and design for their purchase.
Improved User Experience:
Having customization options empowers customers to tailor their furniture to their exact specifications, promoting an engaging and interactive experience. Architects, designers, dealers, and end customers can order custom furniture for various rooms and purposes. These include living rooms, bedrooms, retail displays, and office or remote work furniture.
Real-Time Pricing:
CPQ embedded in ERP software for furniture manufacturing plays a pivotal role in price quoting. It calculates the cost of the custom configuration in real time, considering chosen options, materials, labor, and other factors. This is not only easier for the manufacturer but also ensures that the customer gets accurate pricing upfront.
Accurately Detailed Quotes:
CPQ as part of your ERP manufacturing software determines the cost of the order and then creates a detailed quote. The quote includes the final price, specifications, and delivery timeframe. It serves as a formal proposal for the customer, streamlining an efficient and transparent transaction. It also allows customers to review and make any necessary adjustments before finalizing their order.
Read more:
>> 7 Ways Product Configuration Software Simplifies Manufacturing
>> Why Cabinet and Furniture Manufacturers Need CPQ Software
5 Benefits of ERP CPQ Software for Furniture Manufacturing
Having CPQ tools integrated within your enterprise resource planning (ERP) system offers a multitude of benefits for furniture manufacturers:
1. Faster Order Processes:
ERP with CPQ software for furniture manufacturing streamlines order processing. It reduces customer service time and the potential errors from manual data re-entry. This results in faster order fulfillment, increased productivity, and reduced costs in the overall furniture manufacturing process.
2. Reduction in Errors:
Automation of the configuration tools and pricing processes minimizes the likelihood of errors in quotes and orders. Fewer errors mean fewer order corrections, returns, and material shortages, saving both time and resources and increasing customer satisfaction.
3. Connection with Production Scheduling:
ERP with built-in CPQ software for furniture manufacturing enables real-time communication with production scheduling. CPQ ensures seamless coordination, automatically merging furniture orders into the production schedule, allowing for optimal resource allocation and timely delivery.
4. Monitoring Materials Inventory:
CPQ tools in your ERP software for furniture manufacturing provide better control and monitoring of materials inventory within the operation. Manufacturers can easily track stock levels, automatically generate purchase orders to replenish materials as needed, and minimize excess inventory, resulting in significant cost savings. Learn more in this blog post, How CPQ Improves Materials Management.
5. Data-Driven Decision-Making:
ERP systems with CPQ software for furniture manufacturing provide furniture manufacturers with data analytics for informed decision-making. Using real-time data helps improve strategies and product offerings by understanding customer preferences, production efficiency, and market trends.
How Furniture Manufacturers Can Streamline Operations
Furniture manufacturers can streamline their sales, ordering, production, and delivery processes fairly easily with the right tools. By adopting an ERP system with built-in CPQ software for furniture manufacturing you can optimize operations and implement efficient strategies. Here are some key steps and approaches to achieving this:
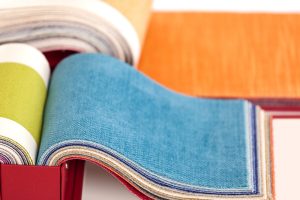
Customization is often an important part of the furniture buying experience.
Implement CPQ Tools for Manufacturing:
CPQ is a valuable tool for streamlining sales, ordering, and production. This manufacturing technology allows customers to customize their furniture orders, receive accurate pricing, and generate quotes quickly. When integrated with your ERP system, you are ensured of smooth order processing and accurate delivery data. An even better long-term solution is an ERP system with CPQ built in.
Utilize ERP Software for Furniture Manufacturing:
An ERP system acts as the backbone of your operations. It provides a centralized platform to manage and monitor business operations including inventory, furniture production scheduling, financials, and customer data. Friedman’s Frontier ERP software for furniture manufacturers provides real-time visibility and data-driven decision-making. Frontier ERP is ideal software for furniture manufacturing thanks to its robust product configurator and CPQ tools.
Automate Sales and Customer Relationship Management (CRM):
Implement a CRM system to effectively manage leads, track customer interactions, and maintain a sales pipeline. Automation can help identify and nurture potential customers for different types of furniture purchases. These purchases can include office furniture systems, remote work furniture, or retail display furniture.
Optimize Production Processes:
In addition to ERP with CPQ software for furniture manufacturing, consider adopting lean manufacturing principles and practices to streamline furniture manufacturing operations. This involves minimizing waste, improving efficiency, and maintaining a continuous flow of work. Lean methodologies can help reduce lead times and production costs.
Incorporate a Warehouse Management System (WMS):
A WMS is an inventory management system that helps by optimizing storage, order picking, and shipping processes. WMS systems enable you to track inventory levels in real time, minimizing stockouts and overstock situations. Friedman Frontier ERP has an integrated WMS module that expands on the warehouse tools already included with the software.
Optimize Supply Chain Management:
Optimize your supply chain by collaborating closely with suppliers to ensure timely delivery of materials. Accessing real-time order data and inventory levels allows you to reduce holding costs and improve material availability.
Implement Quality Control and Assurance Processes:
Furniture manufacturers should also implement a robust quality control and assurance process. By identifying and rectifying defects early in the production process, companies reduce rework and warranty claims. Software for furniture manufacturing like ERP CPQ software also helps to reduce returns because of its real-time data management and customization options.
Optimize Delivery Routes:
Use route optimization software to plan efficient delivery routes and schedules. This minimizes fuel costs, reduces delivery times, and enhances customer satisfaction.
Increase Employee Training:
Train your staff to use all software and equipment efficiently. A well-trained workforce is essential for smooth operations, especially in software for furniture manufacturing. Opt for a system with a modern look and feel for today’s younger workforce. Just don’t choose style over substance.
Adopt Continuous Improvement Goals:
Establish a culture of continuous improvement within your furniture manufacturing operation by setting objectives to meet organizational goals. Regularly assess and refine your processes to identify areas for improvement and eliminate bottlenecks and inefficient processes.
Conclusion
The furniture industry uses CPQ tools with ERP software for furniture manufacturing to meet the needs of modern consumers. This manufacturing technology simplifies the creation of custom furniture orders. It has several advantages, including faster order processing, fewer mistakes, improved production scheduling, and better materials inventory management. The bottom line: It helps manufacturers stay competitive and gives customers the personalized solutions they want.
The future of furniture production lies in embracing these cutting-edge technologies, ensuring efficient operations, and delivering superior, customized products to a discerning market. CPQ-integrated ERP software for furniture manufacturing provides a wide array of benefits. Contact us today about Friedman Corporation’s software for furniture manufacturing and get ready to streamline your operations!