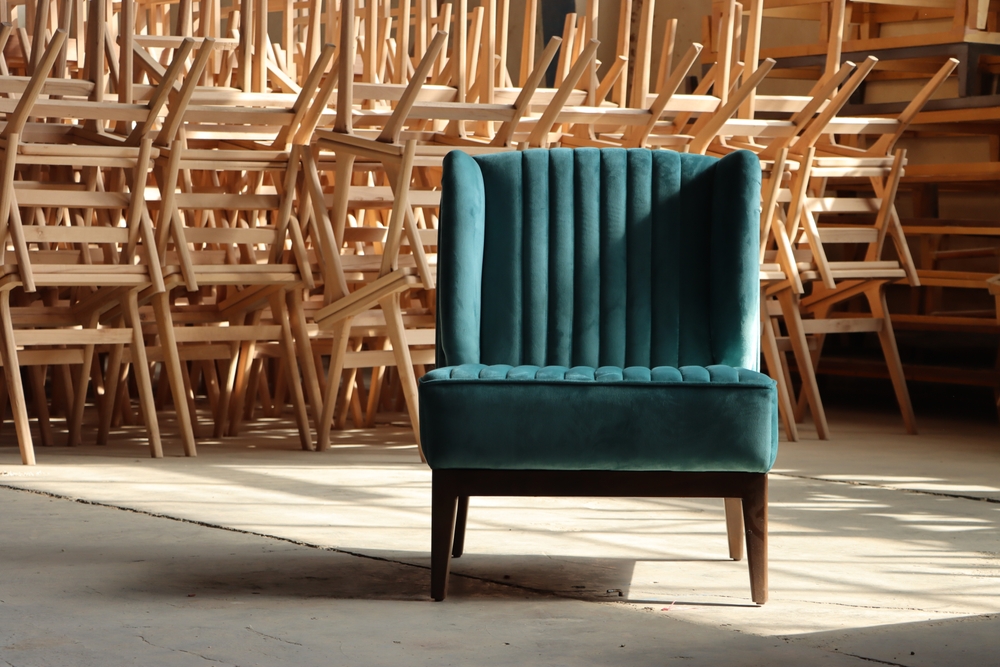
Technology is present in nearly every facet of our lives, from smart homes and window coverings to production tracking and automated manufacturing processes. While tech availability is widespread, it must be used properly to realize the biggest benefits in business. This is especially true for residential and contract furniture manufacturers seeking streamlined operations. Therefore, adopting a benefit-rich furniture ERP system is not just a luxury—it’s a necessity.
In this article, we’ll delve into common challenges that can hinder operations for furniture manufacturers. We’ll also explore the 10 must-have features of a modern ERP system for operational efficiency.
The Challenge: Hurdles to Efficiency in Furniture Manufacturing
Both residential and contract furniture manufacturers face unique challenges that can disrupt production flow and diminish overall performance. Understanding these obstacles is the first step towards mitigating them and moving towards a more streamlined operation.
Industry Uncertainty
The home furnishings industry is experiencing weak consumer interest. Industry experts argue that furniture companies must do more to promote sales and deploy a new effort in product development. One expert lamented, “Too many of our stores and online retailers are looking at 2025 as being more of the same! We are not seeing the new product introductions that we need to spur consumer attention and interest this coming Spring.”
The contract furniture industry is expected to hit $67 billion in 2025. The projected growth during the forecast period is driven by several key factors, including a focus on wellness and ergonomic design, demand for flexible and modular furniture, and the growing popularity of customizable solutions. Notable trends include the integration of technology, the rise of smart furniture, the adoption of virtual and augmented reality in the design process, and ongoing innovation in sustainable materials.
Meanwhile, the furniture industry as a whole continues to wrestle with inventory imbalances that affect operational efficiency. Plus they face a myriad of challenges, including high shipping rates, reciprocal tariffs, and persistently high inflation.
Complex Supply Chains
Furniture manufacturing often involves dealing with multiple suppliers, diverse raw materials, and fluctuating costs. Managing these components without a centralized system can lead to miscommunication, delayed shipments, and increased overhead costs. An advanced furniture ERP system integrates supply chain management into its processes. Doing so provides real-time insights that help manufacturers improve operational efficiency by reducing delays and minimizing inventory issues.
Customization Demands
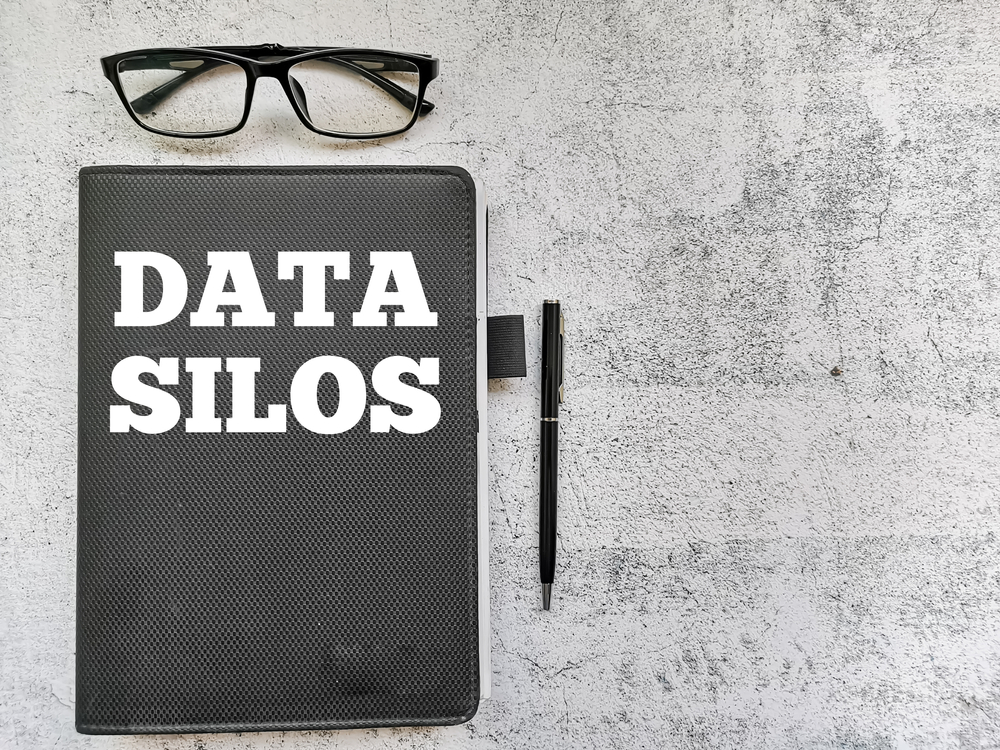
When data is pulled from different systems or departments, it leads to data silos that often include duplicated or inaccurate information.
Residential customers demand personalized furniture that fits their unique tastes and spatial requirements. While contract buyers usually go with a cohesive, yet custom look driven by corporate standards. This surge in customization has driven the need for a furniture ERP that can seamlessly handle complex orders. However, without a powerful product configurator, customizing products can slow down the production process and lead to errors, ultimately affecting customer satisfaction.
Production Inefficiencies
High-volume or batch production can quickly become a logistical nightmare without proper oversight. Factors such as machine downtime, workforce scheduling, and quality control discrepancies can all lead to bottlenecks. When these elements are not effectively managed, it becomes increasingly difficult to improve operational efficiency and meet customer deadlines.
Data Silos and Inaccuracies
Data is often scattered across various departments and systems at many traditional furniture manufacturing plants. There is also a risk of information being entered manually and incorrectly. This fragmentation can lead to decision-making based on outdated or inaccurate information. The result is inefficient production planning and wasted resources.
Integration with New Technologies
With the rapid pace of technological change, integrating new software solutions with legacy systems poses a significant challenge. Manufacturers must ensure that any new furniture ERP solution can work in harmony with their existing infrastructure. This includes modern product configurator tools to truly harness the benefits of digital transformation.
10 Frontier ERP Features to Improve Operational Efficiency
Modern ERP solutions are designed to tackle the complexities of furniture manufacturing head-on. Below are the ten essential Frontier ERP features that every manufacturer can benefit from.
1. Integrated Inventory Management
Efficient inventory management is the cornerstone of successful furniture production. A Frontier ERP provides real-time tracking of raw materials, work-in-progress items, and finished goods. This integration ensures that inventory levels are optimized, reducing both overstock and stockouts. By maintaining accurate inventory data, manufacturers can better plan production schedules, reduce holding costs, and ultimately improve operational efficiency.
2. Advanced Production Scheduling
Production scheduling is critical in high-volume environments. Frontier ERP offers advanced scheduling tools that consider machine availability, labor allocation, and production deadlines. This functionality allows manufacturers to allocate resources more effectively, minimizing downtime and maximizing output. Advanced production scheduling ensures that production cycles are streamlined, keeping the factory floor running smoothly and saving time even for batch runs.
Let’s say the manufacturer receives multiple sales orders requiring the same fabric. Frontier’s Cut Part Processing and Master Production Schedule allows for multiple cuts from the same fabric in the same batch process. This helps eliminate material waste and reduces production time.
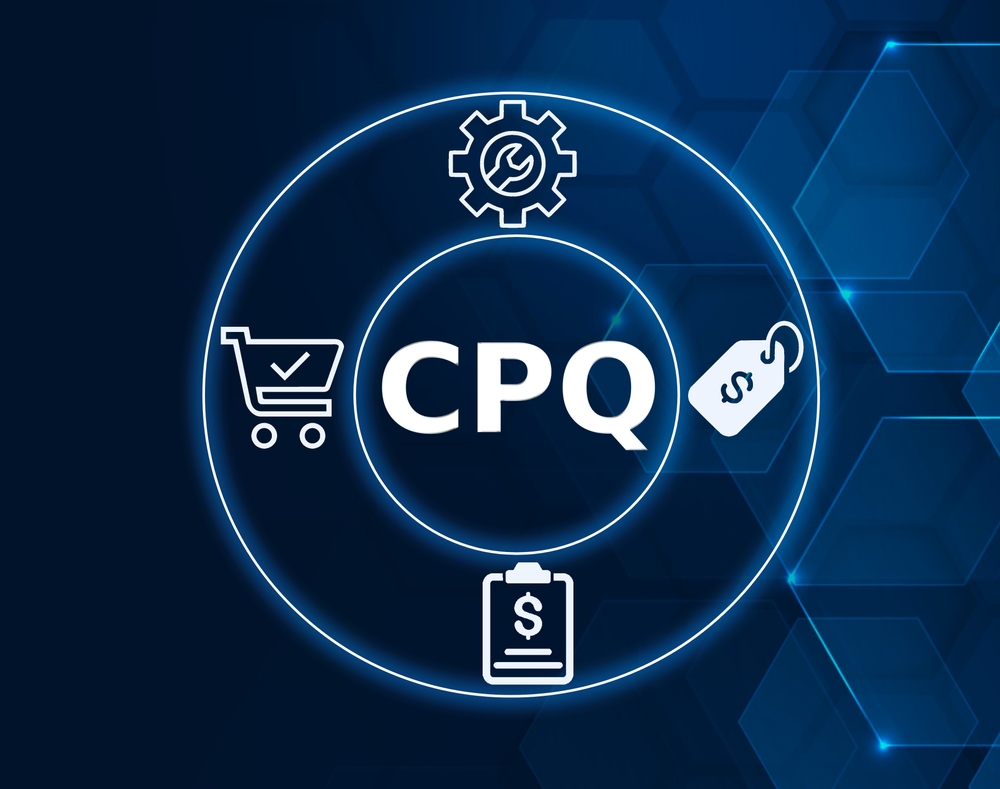
CPQ software is a must-have for a furniture ERP to provide the most efficient order management and automated workflows.
3. Comprehensive Order Management
Handling orders manually or through disparate systems can lead to errors and delays. A centralized order management system within Frontier ERP can automate the entire order lifecycle—from order entry and processing to delivery. With seamless integration between sales, production, and shipping, furniture manufacturers can ensure each order is handled promptly and accurately. This integration is key to improving operational efficiency by reducing administrative overhead, improving order fulfillment, and ensuring customer satisfaction.
4. Dynamic Product Configurator
One of the most transformative features for modern furniture makers is a dynamic product configurator. This tool empowers customers to personalize their furniture designs and receive detailed quotes faster, while ensuring that the shop floor receives accurate and detailed specifications for production
Frontier’s parametric product configurator integrates with the ERP system’s CPQ software to automatically update design parameters and production requirements. This reduces errors, streamlines the manufacturing process, and enhances the customer experience. Plus, Frontier’s built-in CPQ also improves operational efficiency by reducing the need for manual intervention and rework.
5. Financial Management and Cost Tracking
In any manufacturing environment, keeping a close eye on financial performance is essential. Frontier ERP includes modules for financial management, cost tracking, and budgeting. These tools enable furniture makers to monitor expenses in real time, analyze profitability by product line, and make informed decisions that align with their financial goals. Effective financial management is critical to improve operational efficiency by ensuring that resources are allocated wisely and that operating costs are maintained.
6. Supply Chain Integration
Given the complex supply chains in the furniture industry, integration with suppliers and logistics providers is a must. Frontier’s supply chain management capabilities can seamlessly connect with external systems, providing real-time updates on raw material availability, shipping statuses, and supplier performance. This connectivity allows manufacturers to anticipate disruptions and adjust their production schedules accordingly. Improved supply chain visibility directly translates into enhanced operational efficiency and reduced downtime.
7. Quality Control and Compliance
Maintaining high-quality standards is vital for retaining customer trust and meeting regulatory requirements. Frontier ERP systems offer integrated quality control capabilities for monitoring each stage of the production process. It can track quality metrics, flag deviations, and provide actionable insights to ensure compliance with industry standards. A focus on quality control not only reduces waste but also increases operational efficiency by minimizing rework and returns.
8. Business Intelligence and Analytics
Data is the new currency in manufacturing. Therefore, a modern ERP should offer robust business intelligence (BI) and analytics tools to improve efficiency. These features enable manufacturers to transform raw data into actionable insights. One example would be piece labor reporting, Management can analyze how long cut/sew tasks take for a line of sofas or even individual pieces in the product line.
BI tools help decision-makers understand where improvements can be made, from identifying production bottlenecks to analyzing sales trends. With detailed analytics, manufacturers can fine-tune business processes, forecast demand, and strategically plan for the future.
9. Mobile Access and Cloud Integration
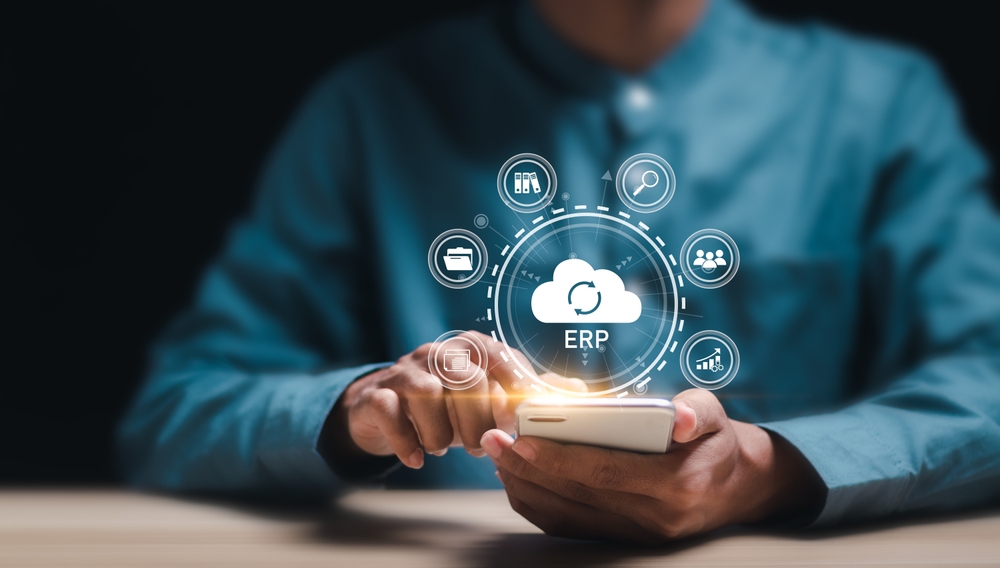
Frontier offers the best ERP for manufacturing that is tailor-made for the furniture industry, whether you want to deploy on-premise, in the cloud, or a hybrid of the two.
In today’s fast-paced environment, having access to real-time data on the go is indispensable. Cloud-based Frontier ERP systems with mobile access allow staff to stay connected, regardless of their location. Whether it’s contacting customer service, entering dealer orders, or monitoring production status, mobile access ensures that critical information is always at your fingertips. This flexibility not only accelerates decision-making but also improves operational efficiency by reducing delays associated with traditional, on-premise systems.
10. Customizable and Scalable Architecture
Every furniture manufacturer is unique, and a one-size-fits-all ERP solution is rarely sufficient. A customizable and scalable ERP system like Frontier ERP allows businesses to tailor the software to their specific needs. Scalability is crucial for maintaining efficiency as production volumes increase and market demands evolve. Whether it’s adding modules for additional production lines or modifying workflows, a Frontier system grows with your business.
Leveraging ERP for Long-Term Success
Investing in a comprehensive ERP system is a strategic move that lays the foundation for long-term success. By addressing common operational challenges and incorporating advanced features, manufacturers can transform their production processes and gain a competitive edge in the market.
Embracing Technological Transformation
As the furniture manufacturing landscape continues to evolve, companies that fail to embrace digital transformation risk falling behind. Modern ERP systems are designed to integrate seamlessly with emerging technologies. By adopting these technologies, manufacturers can not only improve operational efficiency but also foster a culture of innovation that drives continuous improvement.
The ROI of a Modern ERP System
The initial investment in a quality ERP software can be significant for some companies. However, the long-term benefits far outweigh the costs. Reduced production errors, optimized inventory levels, and enhanced customer satisfaction translate into tangible savings and increased profitability. Frontier offers the best ROI with faster adoption while maintaining a high standard of quality.
Future-Proofing Your Business
In a rapidly changing market, flexibility and adaptability are paramount. A scalable ERP system ensures that your business can evolve in response to new challenges and opportunities. A modern ERP solution like Frontier is key for strong and forward-looking furniture manufacturers. It aids in developing new markets, innovative products, and integrating the latest technology.
Conclusion
The ability to improve operational efficiency is directly linked to a company’s success and longevity. Residential and commercial furniture manufacturers are no exception. A furniture ERP system with a user-friendly interface and equipped with advanced features can be a game-changer for high-volume manufacturers. By addressing the common challenges of complex supply chains, customization demands, and production inefficiencies, manufacturers can unlock new levels of productivity and profitability.
The journey towards improving operational efficiency begins with a strategic focus on technology, including a furniture ERP system from Frontier. Whether you are new to the world of ERPs or looking to enhance an existing system, Frontier is an investment in the future of your business.
The time to act is now—unlock the full potential of your operations and secure a future of growth and efficiency. Would you like to learn more about how Frontier ERP can help your furniture shop become more efficient? Click the button below or stop by and see us at AWFS® Fair 2025 in July!
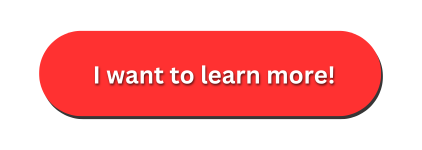
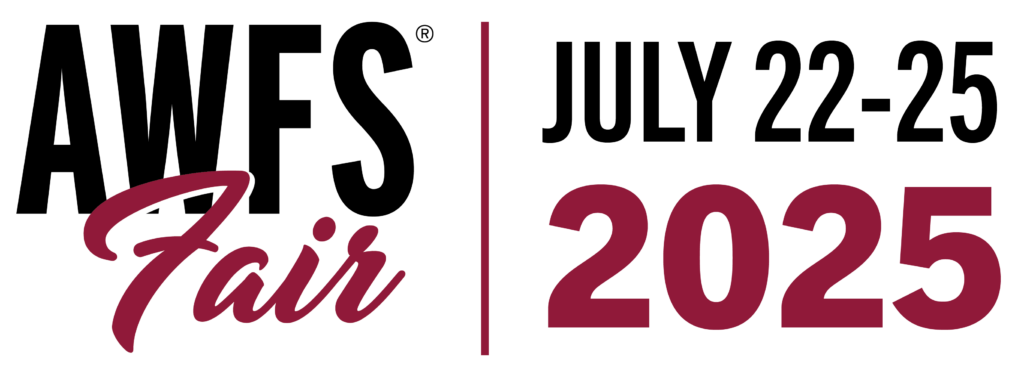