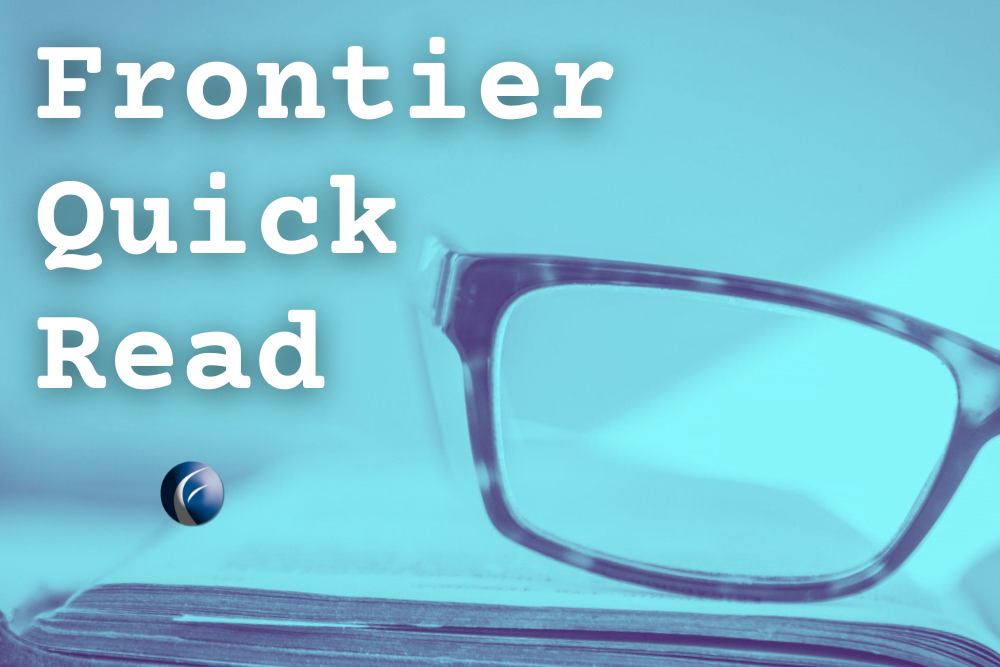
Effective work order management is critical for keeping production on track, controlling costs, and ensuring smooth manufacturing operations. Yet, many manufacturers struggle with outdated or manual work order processes. Those can lead to delays, inaccurate job costing, and a lack of real-time visibility. Without a streamlined system, tracking production progress, labor hours, and scrap can quickly become overwhelming.
ERP workflow automation can make a difference in this situation. A top ERP system for manufacturing, like Frontier ERP, automates work order processes for greater efficiency and visibility. To learn more, we’ll dive into common work order management issues for manufacturers and explore Frontier ERP solutions.
Common Challenges in Work Order Management
Many manufacturers struggle with outdated or manual work order management processes. These challenges create inefficiencies that impact productivity and profitability.
1. Lack of Real-Time Visibility
Manufacturers need to know the status of every work order at any given moment. Manually-tracked work orders don’t provide an order’s progress onscreen or accurate production reports. Managers may not realize when a job is delayed, which can cause missed deadlines and production bottlenecks.

Don’t let your production department get bogged down by manual entries. Look to Frontier ERP workflow automation for better efficiency and enhanced production reports.
2. Inaccurate Job Costing
Understanding job costs is essential for maintaining profitability. But without an automated system, it’s easy to miscalculate labor, materials, and overhead costs. If job variances (the difference between estimated and actual costs) go unnoticed, manufacturers may struggle to identify inefficiencies and control expenses. Inaccurate job costing can also lead to incorrect product costing, hurting the bottom line.
3. Production Delays and Inefficiencies
Work order processes must be well-coordinated between sales, production, and scheduling teams. When work orders are created manually or take too long to release, production can slow down. These delays can result in idle workers, missed deadlines, and increased costs.
4. Limited Reporting Capabilities
Some manufacturers lack detailed production reports that track key metrics like scrap rates, labor efficiency, and job completion. Without this data, it’s hard to identify trends and make informed decisions to improve operations.
5. Complex Work Order Closing Process
Closing work orders involves gathering final costs, generating job variance reports, and ensuring accurate financial records. When manufacturers don’t have an automated process, closing work orders can be time-consuming and prone to errors. Inaccurate financial reporting can create major issues for long-term planning and profitability analysis.
How Frontier ERP Solves Work Order Management Challenges
Frontier simplifies work order management and automates ERP workflows, reducing inefficiencies and improving accuracy for manufacturers of all sizes. Here’s how:
1. Full Control Over Work Order Lifecycle
With Frontier ERP, manufacturers can manually create, release, and print work orders while maintaining full control of manufacturing processes. This ensures work orders are properly scheduled, assigned, and executed without unnecessary delays.
2. Real-Time Production and Scrap Reporting
Workstation-based reporting screens allow workers to log production progress as it happens. This ensures that supervisors and managers have real-time visibility into work order status. Additionally, production reports capture data on scrap, helping manufacturers identify inefficiencies and reduce waste.
3. Accurate Labor Tracking for Cost Control
Tracking labor costs is essential for managing profitability. Frontier ERP allows manufacturers to record labor hours per order or production line directly within the system for enhanced efficiency. This ensures that labor costs are accurately linked to specific work orders, making job costing more precise and reliable.
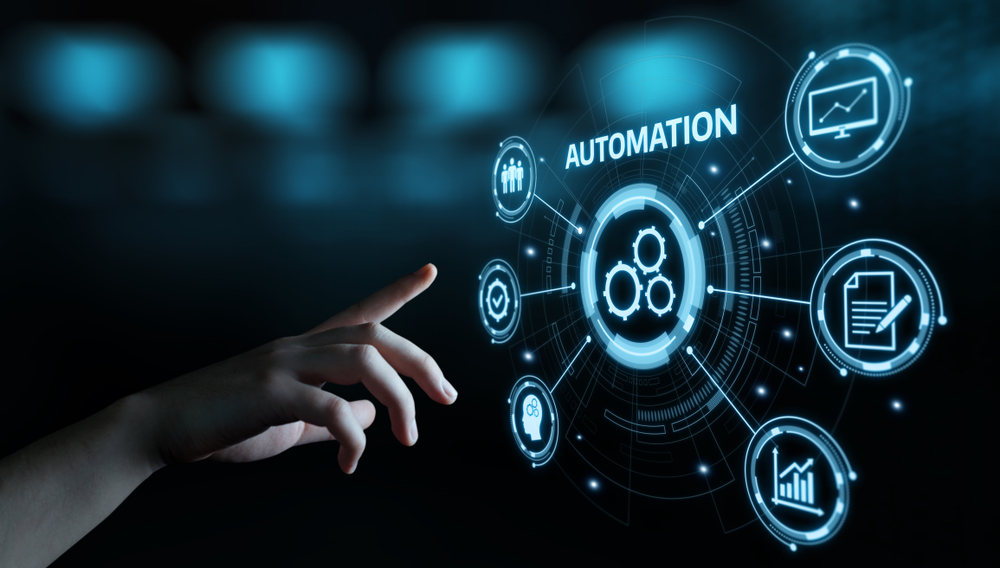
ERP workflow automation is a must for today’s manufacturers to be successful and stay ahead of the competition.
4. ERP Workflow Automation for Work Order Closing
Closing a work order involves finalizing job costs, generating reports, and ensuring financial accuracy. With ERP workflow automation, Frontier streamlines this process. It automatically generates job variance reports, tracks final material and labor costs, and ensures all financial data is accurate. This eliminates manual errors and saves time during the work order closing process.
5. Seamless Integration with Other ERP Functions
Work orders don’t exist in isolation. They affect sales, financial, production scheduling, procurement, and inventory management. Frontier ERP integrates work orders with other core functions, creating a seamless flow of information across the entire business. This eliminates data silos and ensures that all departments are aligned and can make data-driven decisions.
Benefits of ERP Workflow Automation in Work Order Management
A 2021 report from automation software maker Zapier found that 94% of small and medium-sized business (SMB) workers surveyed said they perform repetitive, time-consuming tasks. The report also noted that 90% of knowledge workers found that automation improved their jobs, and 66% said automation has made them more productive.
No matter their size, manufacturers who use Frontier ERP for work order management experience several key benefits:
- Improved Efficiency – ERP workflow automation of orders reduces delays and keeps production on schedule.
- Increased Visibility – All departments have visibility to real-time data across the entire business.
- Better Cost Control – Real-time tracking of labor, materials, and overhead costs ensures accurate job costing.
- Informed Decision-Making – Detailed production reports provide insights into improved productivity, scrap rates, and job performance.
- Reduced Errors – Automated work order closing eliminates manual mistakes in financial reporting.
- Seamless Communication – Integration with other ERP functions ensures that production, inventory, and financial teams stay aligned.
Conclusion
For manufacturers looking to optimize work order management, improve production reporting, and leverage ERP workflow automation, Frontier ERP provides a powerful solution. By automating key processes, providing real-time insights, and ensuring accurate job costing, Frontier helps manufacturers boost productivity and profitability for business success.
Are you ready to take control of your work orders? Contact us today to learn how Frontier ERP can streamline your operations!