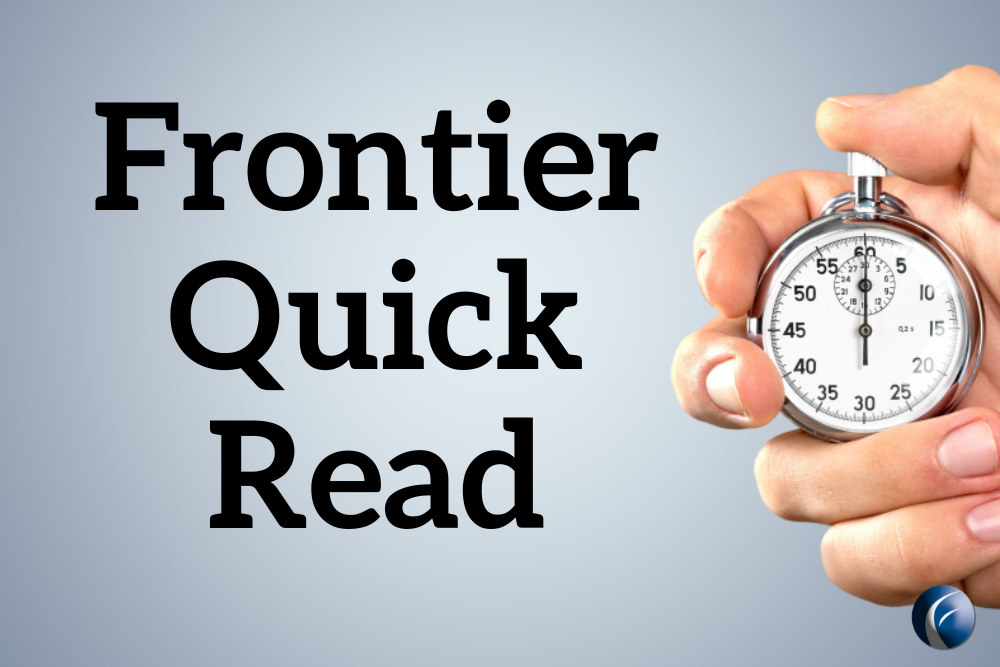
Managing distribution requirements across multiple plants is a complex challenge for manufacturers and distributors. When material demand shifts from one plant or distribution center (DC) to another, inefficiencies can arise. These can lead to inventory imbalances, stockouts, or excess holding costs. An effective Distribution Requirements Planning (DRP) system in these environments is essential to maintaining a smooth supply chain.
Enterprise Resource Planning (ERP) systems play a crucial role in ensuring that DRP is executed effectively by providing visibility, automation, and control over inter-plant shipments. This article explores the challenges of managing distribution requirements across multiple locations and how ERPs, particularly Frontier ERP, address these complexities.
Challenges of Distribution Requirements Planning in Multi-Plant Environments
When a company operates multiple plants or distribution centers, demand for materials often originates in one location but must be fulfilled by another. This presents several logistical challenges:
- Demand Uncertainty – Forecasting demand for multiple locations can be difficult, especially when customer orders fluctuate or seasonal demand impacts inventory needs.
Supply Chain Coordination – Ensuring that the right products are available at the right location and time requires seamless coordination between procurement, production, and logistics teams.
- Inter-Plant Transfers – Moving inventory between locations involves tracking shipments, transferring ownership, and accounting for gains and losses.
- Overstock and Stockouts – Without proper planning, some locations may have excess inventory while others face shortages, leading to inefficiencies and increased costs.
- Visibility and Communication – Real-time visibility into stock levels, planned transfers, and production schedules is necessary to make informed decisions and prevent bottlenecks.
To address these challenges, ERPs integrate distribution functionality to manage inventory distribution efficiently.
How ERPs Enhance Multi-Plant Distribution
ERPs provide a centralized platform for managing distribution requirements planning by integrating demand forecasting, supply chain coordination, and real-time data analysis. Here’s how ERPs help with optimization:
- Automated Demand Planning – ERPs analyze historical sales data, customer orders, and market trends to forecast demand accurately across multiple locations.
- Optimized Inventory Allocation – With real-time stock level visibility, ERPs ensure that inventory is distributed efficiently, preventing both shortages and excess stock.
- Inter-Plant Shipment Coordination – ERPs facilitate the execution of inter-plant transfers, tracking shipments from origin to destination, and managing transfer costs.
- Seamless Integration with MRP/MPS – Distribution requirements planning within an ERP system works alongside Material Requirements Planning (MRP) and Master Production Scheduling (MPS) to align production with distribution needs.
- Real-Time Supply Chain Insights – ERPs provide dashboards and reporting tools that help planners monitor distribution performance, track key metrics, and make data-driven decisions.
Frontier ERP’s Distribution Requirements Planning Features
Frontier ERP offers a comprehensive distribution requirements module that enhances supply chain efficiency by automating inter-plant demand planning and execution. Here’s how Frontier ERP simplifies materials allocation:
- Planned and Forecasted Demand Management – Frontier ERP’s module controls planned and forecasted demand across multiple plants and DCs. This ensures that every location has the necessary inventory levels to meet projected sales and production needs.
- Automated Execution – The system runs DRP first to create all planned inter-plant demand. Once demand is established, MRP or MPS is run at the supplying plant to generate the necessary planned orders to fulfill requirements. This sequential execution allows for synchronized material movement across all locations.
- Inter-Plant Shipment Management – The module supports the execution of inter-plant transfers, ensuring that shipments are properly tracked and recorded. It automates shipment scheduling, documents transportation details, and minimizes errors associated with manual tracking.
- Ownership and Accounting Control – Frontier ERP provides full management of ownership transfers and gain/loss accounting, ensuring financial accuracy in inter-plant transactions. This feature is critical for businesses that operate across different financial entities or require precise accounting for transferred goods.
- Seamless Integration with MRP – Frontier’s module complements MRP by focusing on the efficient distribution of completed goods while MRP handles raw materials and production scheduling. This ensures that both production and distribution functions operate in harmony.
- Real-Time Updates – Integrated within the Frontier ERP ecosystem, the module supports real-time updates, improving overall supply chain efficiency. Businesses can react instantly to changes in demand, unexpected disruptions, or urgent transfer requests.
- Demand Analysis and Stock Optimization – By analyzing demand trends and aligning distribution schedules accordingly, Frontier ERP minimizes the risks of stockouts and overstock situations. The system continuously refines demand forecasts based on historical data, ensuring optimal replenishment decisions.
- Inventory Level Control Across Locations – Businesses can manage and monitor inventory across all locations, ensuring optimal stock levels are maintained. This visibility allows supply chain managers to balance inventory dynamically, reducing holding costs while maintaining service level commitments.
Conclusion
Managing distribution planning across many plants is a tough job. However, with the right ERP system, manufacturers can improve operations, manage inventory better, and boost supply chain efficiency. Using an ERP-driven approach to DRP helps businesses lower costs and keep inventory balanced across their distribution network.
Frontier ERP’s Distribution Requirements Planning module provides a robust solution by automating demand planning. Would you like to learn more? Let us know!