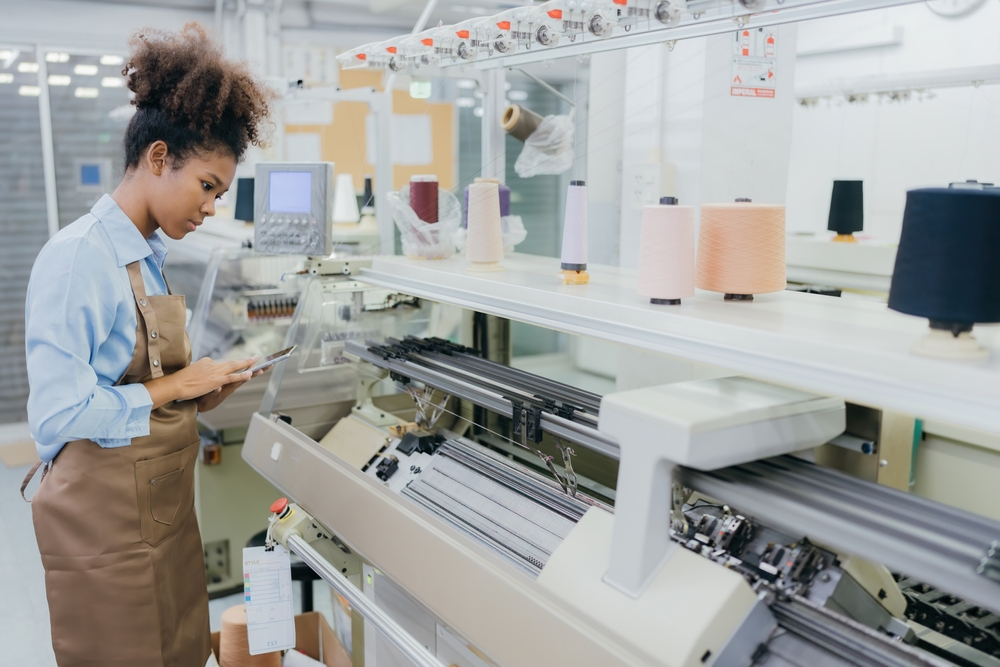
In a highly competitive market, US manufacturers face many economic challenges from global competitors. One such example is the United States government’s de minimis exemption rule. This regulation has significant implications for domestic producers, particularly in the textile industry, where low-cost imports often dominate.
Some manufacturers support this rule for lower-value raw material imports. However, many US textile companies and industry groups object to the regulation because of its negative financial impact on the US textile industry. This article will explore the de minimis exemption rule. It will also discuss current laws, legislative status, and how a textile ERP system can help manufacturers save money.
What is the De Minimis Exemption Rule?
The de minimis exemption rule lets goods worth less than $800 enter the US duty- and tariff-free. Part of the Tariff Act of 1930, it was originally designed to allow travelers to bring souvenirs from abroad and not pay duties. It was later amended to expedite customs processes and encourage world trade. However, this rule has been criticized in recent years for creating an uneven playing field for imports over domestic manufacturers.
Legislative efforts to reform or lower the de minimis threshold are ongoing. Policymakers and industry advocates argue that the current rule disproportionately benefits foreign competitors, particularly in low-cost manufacturing sectors like textiles.
Research has found that a large number of eligible shipments entering the US come from China. The End China’s De Minimis Abuse Act is a bill directed at reform and in support of US manufacturing. The bill ends the de minimis privilege for any goods subject to Section 301 tariffs. It eliminates the privilege for 60% of Chinese imports alone.
While there is momentum for change, the timeline and outcome remain uncertain, leaving manufacturers to navigate the current landscape.
Textile Industry Highs and Lows
The US textile industry has undergone significant transformations since the 1970s. In the 1980s and 1990s, globalization and trade liberalization grew quickly. This led to more competition from countries with lower labor costs. Global policies and agreements allowed cheaper imports to flood the US market, resulting in mill closures and job losses.
Despite these setbacks, the industry began to evolve by focusing on innovation and niche markets. By the early 2000s, the textile industry embraced advanced manufacturing techniques to regain competitiveness. Companies invested in automation, robotics, and cutting-edge materials, such as high-performance fabrics and smart textiles. The sector also found opportunities in technical textiles used in industries like healthcare, automotive, and aerospace.
The COVID-19 pandemic highlighted vulnerabilities in global supply chains, pushing some manufacturers to explore reshoring initiatives. Today, the US textile industry also faces high production costs, a skilled labor shortage, and ongoing supply chain disruptions. However, competition from countries with strong textile industries, like China, India, and Bangladesh, continues to put pressure on domestic manufacturers.
Impact of De Minimis Exemption on the US Textile Industry
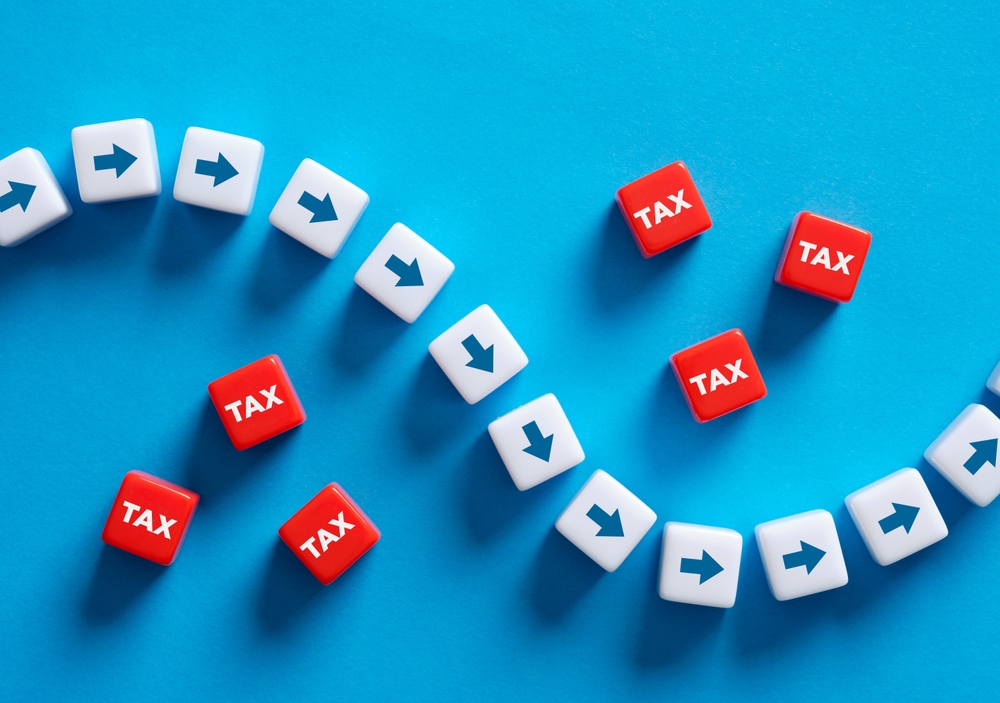
While the future of the US de minimis exemption rule remains unclear, textile manufacturers can still adopt cost-saving measures by using Frontier’s manufacturing ERP system.
The de minimis exemption creates significant challenges for US manufacturers, with its effects rippling across various industries like furniture, window treatments, and apparel. One of the most pressing issues is the problem of unfair competition. By allowing low-cost imports to avoid duties and tariffs, the exemption allows foreign producers to sell their goods for much less. This means they can offer lower prices than domestic manufacturers can.
This results in a market skewed in favor of imports, making it difficult for US companies to compete, especially in price-sensitive markets like textiles. It is harder for them to match the prices of duty-free foreign textiles while remaining profitable.
“We cannot let Chinese-founded e-commerce platforms gain an unfair trade advantage while American businesses play by the rules,” said National Economic Advisor Lael Brainard in a recent news release.
Beyond the loss of market share, the exemption creates operational issues for competing manufacturers. To remain viable, US textile companies are pressured to reduce costs while maintaining the quality that distinguishes them in a crowded marketplace. To survive and thrive, the industry must welcome innovative strategies. These include adopting advanced manufacturing technologies, embracing niche markets, and advocating for fair trade policies.
In addition to these challenges, US textile manufacturers must contend with rising costs in other operational areas. Margins are often razor-thin, and the cost of raw materials, labor, and overhead directly impacts profitability. These additional costs further erode profit margins, forcing companies to decide between maintaining competitiveness and investing in quality, innovation, or workforce development. For US textile manufacturers, these factors may lead to plant closures and moving operations offshore to stay profitable.
Combatting De Minimis Rule Repercussions With a Textile ERP System
Manufacturers must wait to see the results of proposed changes to the de minimis exemption. They also need to consider possible tariff increases from the new presidential administration. In the meantime, these companies can combat the financial pressures by implementing a cost-saving textile ERP system. Here’s how:
Production Management
Automating production processes is a key strategy for improving efficiency in textile manufacturing. Advanced machinery and automated systems can reduce human error, streamline operations, and minimize material waste, resulting in significant cost savings.
By using real-time data systems like textile manufacturing ERP software, you can improve scheduling and effective use of resources. Data-driven insights allow you to adjust production on the fly, meeting demand fluctuations precisely. The combination of automation and real-time monitoring that a textile ERP provides creates a leaner, more responsive production environment, ultimately boosting profitability.
Inventory Management
Effective inventory management is essential to maintaining a competitive edge in the textile industry. Just-in-time (JIT) inventory practices can help you avoid overstocking. It reduces the costs associated with excess storage and unsold goods. This strategy aligns closely with demand forecasting, which uses ERP historical data and market trends to predict future needs.
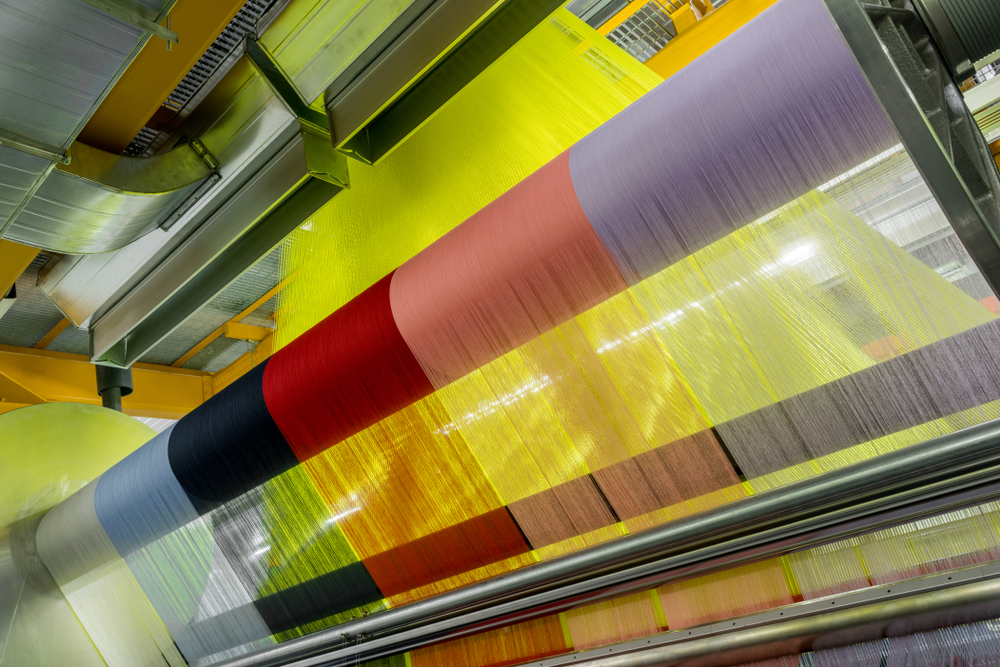
A textile ERP system from Frontier can provide you with advanced features to increase efficiency and streamline operations to combat the impact of the de minimis exemption rule.
By producing only what the market requires, you can better align stock levels, production schedules, and customer demand. It also minimizes waste and improves cash flow by freeing up resources.
Cost Control and Analysis
Modern textile ERP systems provide detailed financial reports that allow you to identify inefficiencies and pinpoint areas for improvement. This visibility enables better pricing strategies, ensuring products remain competitive without sacrificing profitability. By understanding product costing, you can allocate resources more effectively, negotiate better terms with suppliers, and reduce unnecessary expenditures. Regular cost analysis also provides the flexibility to adapt quickly to market changes or unexpected financial pressures.
Enhanced Supply Chain Agility
Supply chain agility is critical for competing in the textile market. Building relationships with multiple suppliers can help manufacturers mitigate risks associated with import competition and disruptions. Diversifying supplier networks ensures consistent access to raw materials and reasonable prices, even in the face of challenges.
Additionally, optimizing logistics and shipping processes with textile ERP software reduces lead times and costs, enabling quicker delivery to customers and improving overall satisfaction. It includes advanced planning and collaboration tools to further enhance supply chain responsiveness. This allows you to adjust rapidly to shifts in demand or supply chain constraints.
Compliance and Reporting
Simplifying government ordinances and industry compliance requirements ensures that manufacturers adhere to all relevant regulations, avoiding costly penalties and disruptions. Textile ERP systems can generate accurate, real-time compliance reports, streamlining audits and enabling better decision-making. These tools also provide the data needed for strategic planning, helping you anticipate regulatory changes and adapt proactively. Effective compliance management not only reduces risk but also strengthens a manufacturer’s reputation in a competitive marketplace.
By improving efficiency, reducing costs, enhancing decision-making, and achieving sustainable growth.
Conclusion
The de minimis exemption rule presents significant challenges for US textile manufacturers. It also underscores the importance of adapting to a changing market. Textile ERPs can help reduce the impact of the de minimis exemption rule by offering a better path to increased efficiency and cost control.
Don’t let the de minimis exemption rule dictate your success. Explore how Frontier’s textile ERP can transform your operations and help you compete globally. Contact us today to learn more and take the first step toward a more resilient future.